I work to create enduring products that serve people.

Stool
2019, personalLightweight, stackable seating made with minimal material use
Work
︎ Sketching
︎ 3D modeling
︎ Prototyping with 3D printing and full-size mockups
︎ Fabrication with Shopbot and Fusion 360
︎ Visualization
︎ Sketching
︎ 3D modeling
︎ Prototyping with 3D printing and full-size mockups
︎ Fabrication with Shopbot and Fusion 360
︎ Visualization
Goals
︎ Lightweight and minimal material use
︎ Stiff and strong
︎ Stackable, up to three high
︎ Foot support
︎ Easily scalable to workbench height
︎ Easy to move
︎ Stable but slim
︎ Non-minimal, funky aesthetic
︎ Lightweight and minimal material use
︎ Stiff and strong
︎ Stackable, up to three high
︎ Foot support
︎ Easily scalable to workbench height
︎ Easy to move
︎ Stable but slim
︎ Non-minimal, funky aesthetic
I set out to make a set of stackable stools to serve as flexible supplemental seating, either for visitors in the design studio or for parties at home.
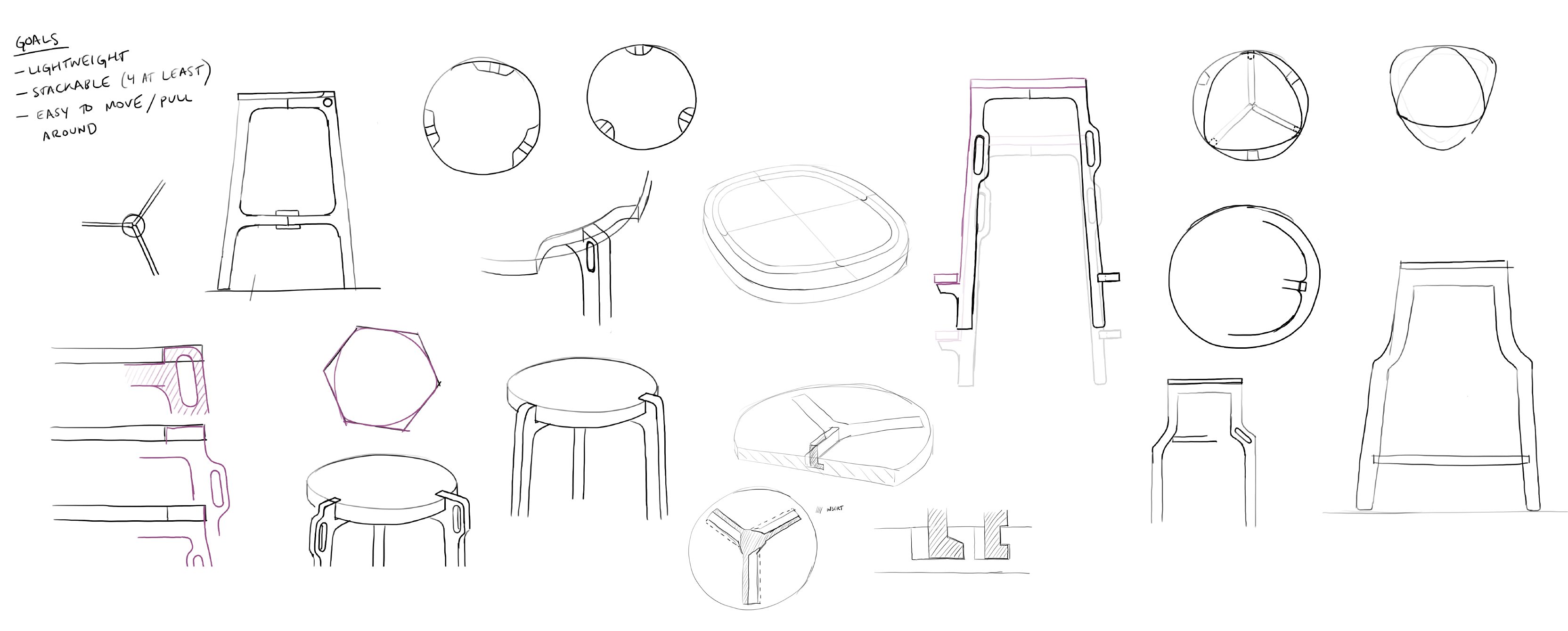

After exploring a number of directions, I chose to pursue a design approach where the seat and leg support ring are created using the same ¼” router-cut profile. This choice allows for minimal material use and lower product cost. In the assembly, the ring is then rotated to avoid interference with the leg. This enables a slimmer assembly with deeper and more efficient stacking.
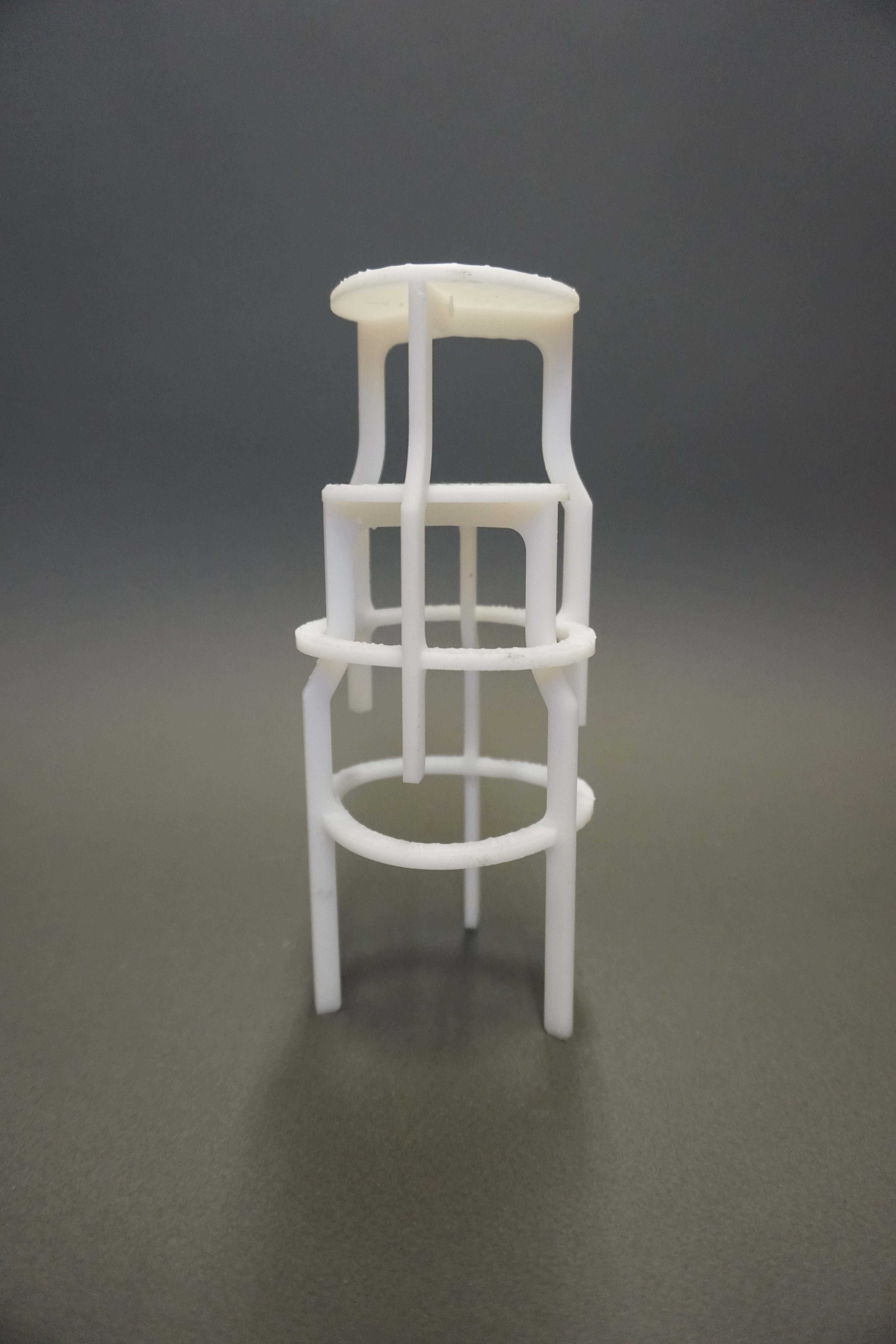
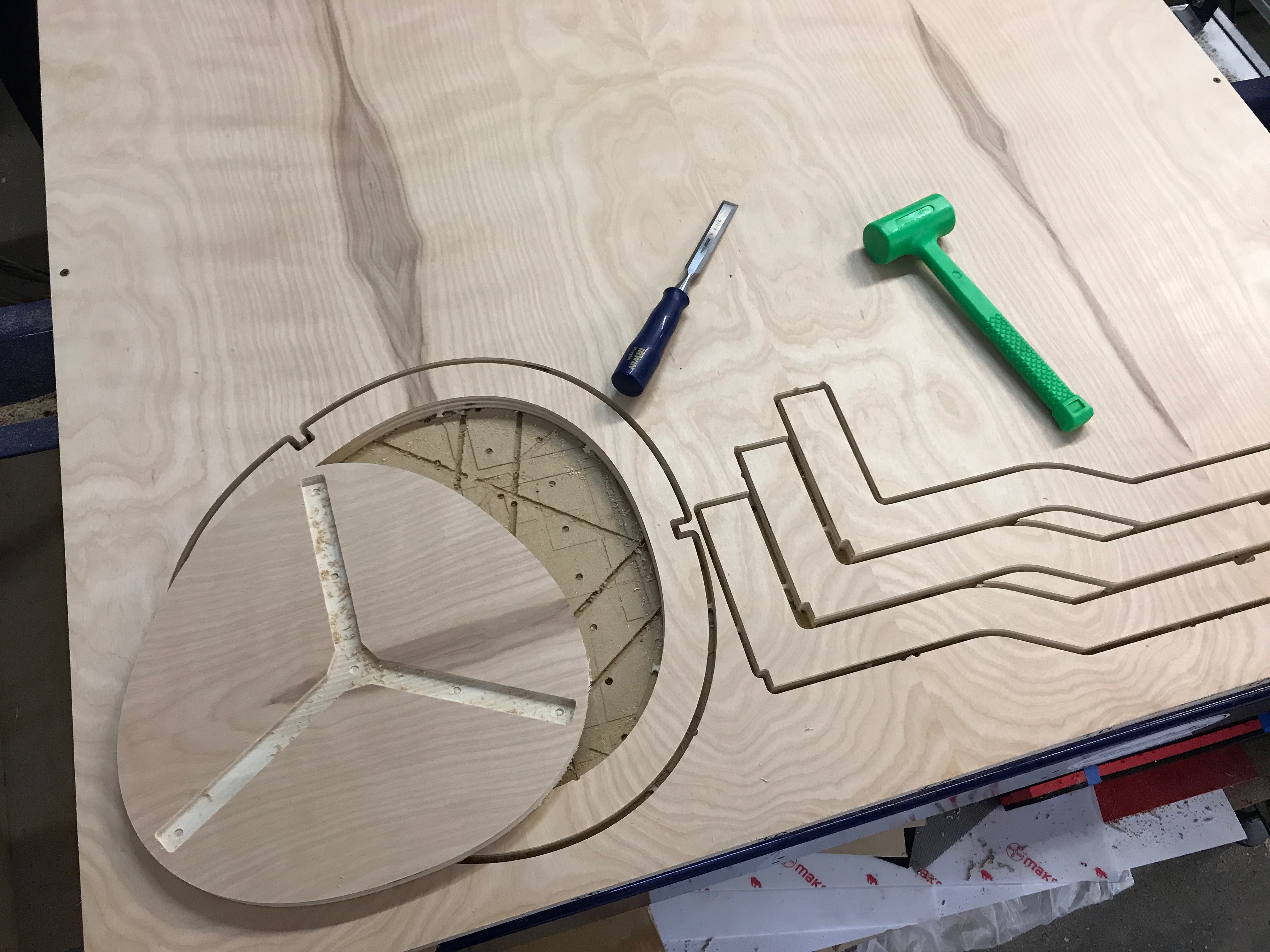
I started with prototyping a design with a trilobular seat and three legs. I used cheap plywood for experimentation runs before committing to higher quality materials.
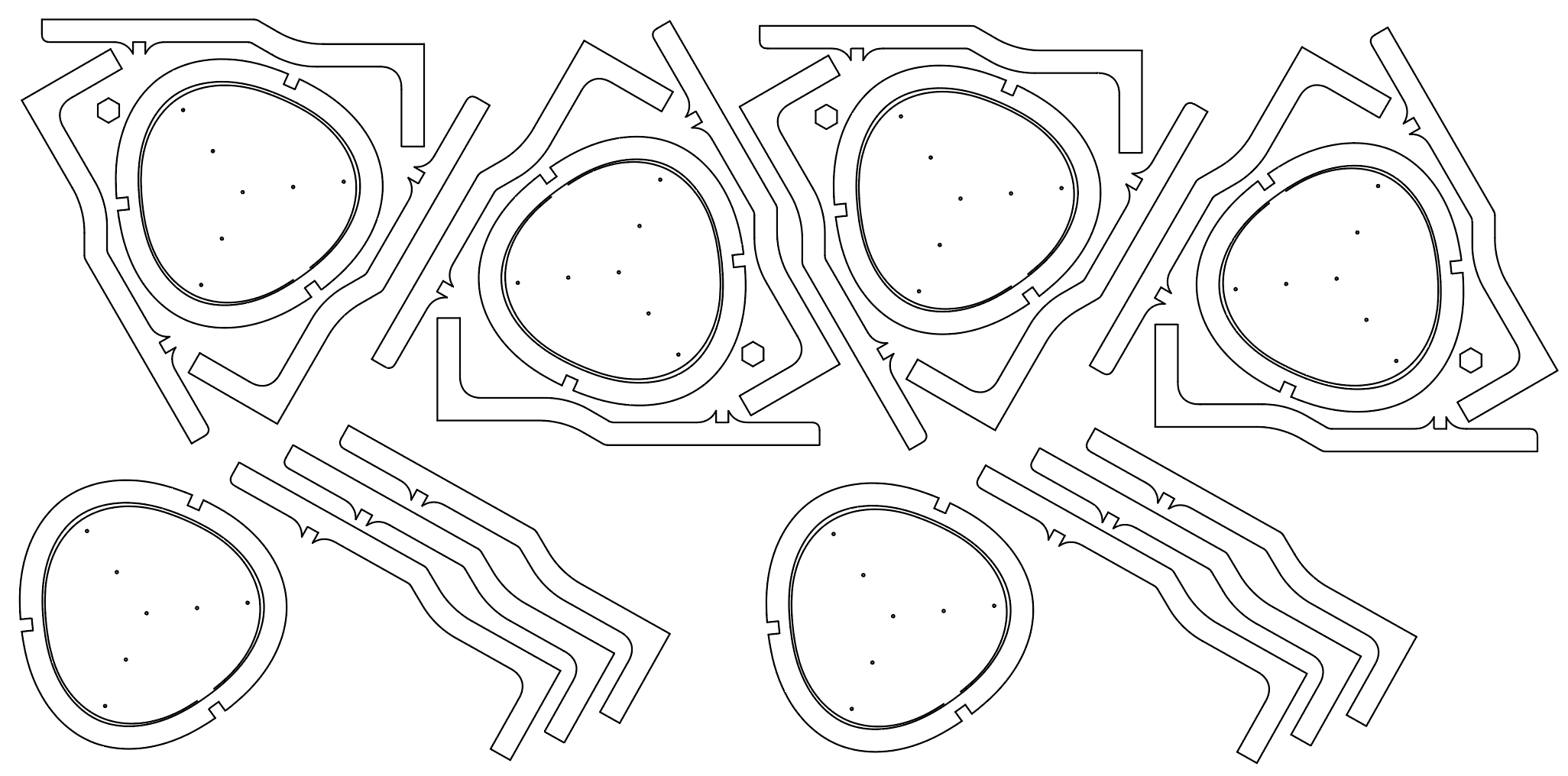
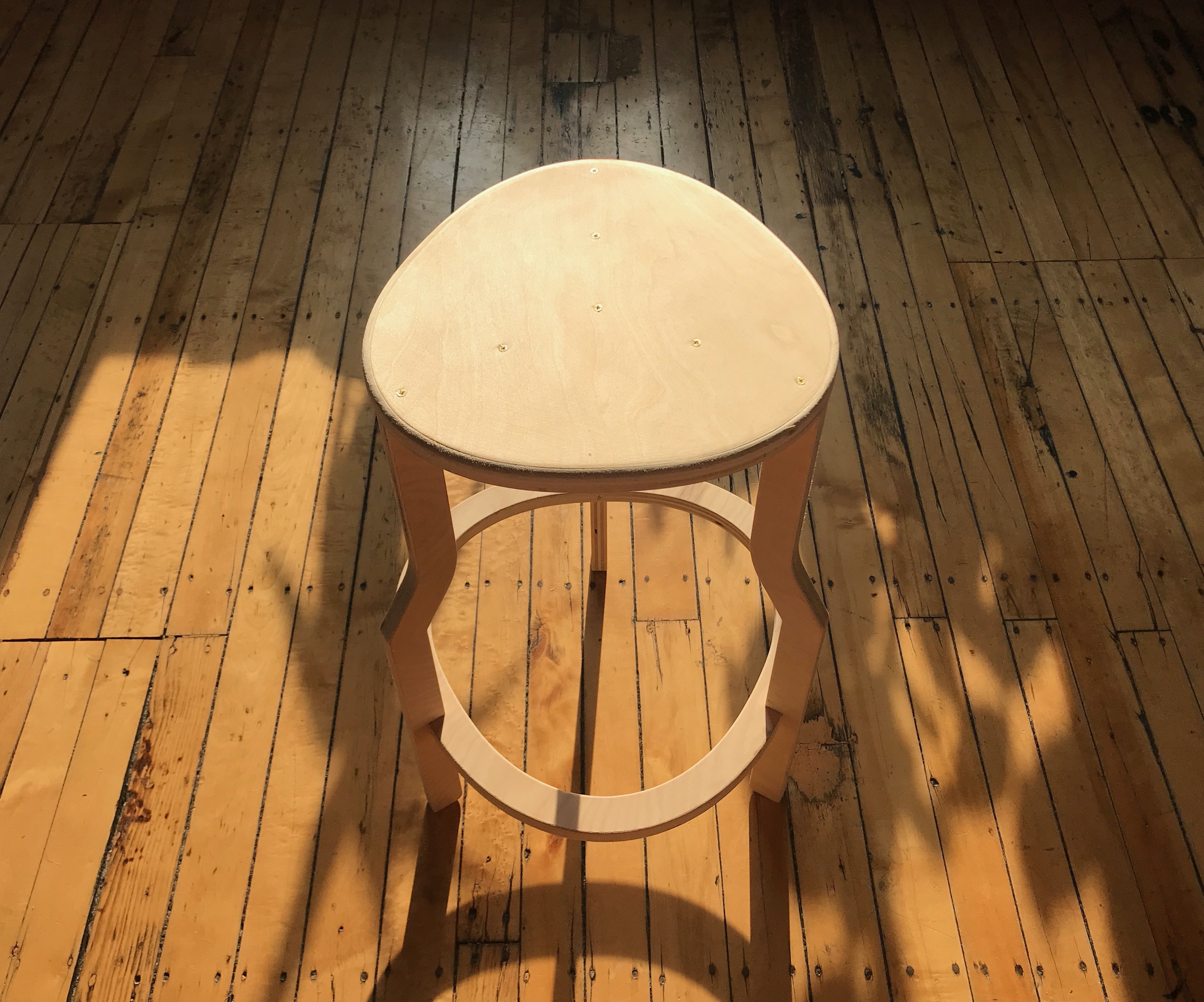
The trilobular design was very efficient with materials and extremely lightweight. However, I decided that the stability improvements of moving to four legs would be worth the detriment to weight and material usage. I also cut a recess into the perimeter of the seat to serve as a handle for better portability.


Six stools can be made from a 4’ x 8’ sheet of plywood. Using 3/4” Baltic Birch B/BB, the material cost per stool comes to only $20.


