I work to create enduring products that serve people.

Shelf
2019, PersonalShelving made from birch plywood, anodized aluminum tube, and glass-filled plastic 3D-printed joinery
Work
︎ Sketching
︎ 3D modeling
︎ Fabrication with Shopbot and Fusion 360
︎ Visualization
︎ Sketching
︎ 3D modeling
︎ Fabrication with Shopbot and Fusion 360
︎ Visualization
Goals
︎ High storage capacity
︎ Open, lightweight aesthetic
︎ Cost effective
︎ High storage capacity
︎ Open, lightweight aesthetic
︎ Cost effective
My goal in this project was to create a highly functional shelving system with minimal visual weight. I wanted to design a large object that would feel as light, airy, and unimposing as possible.
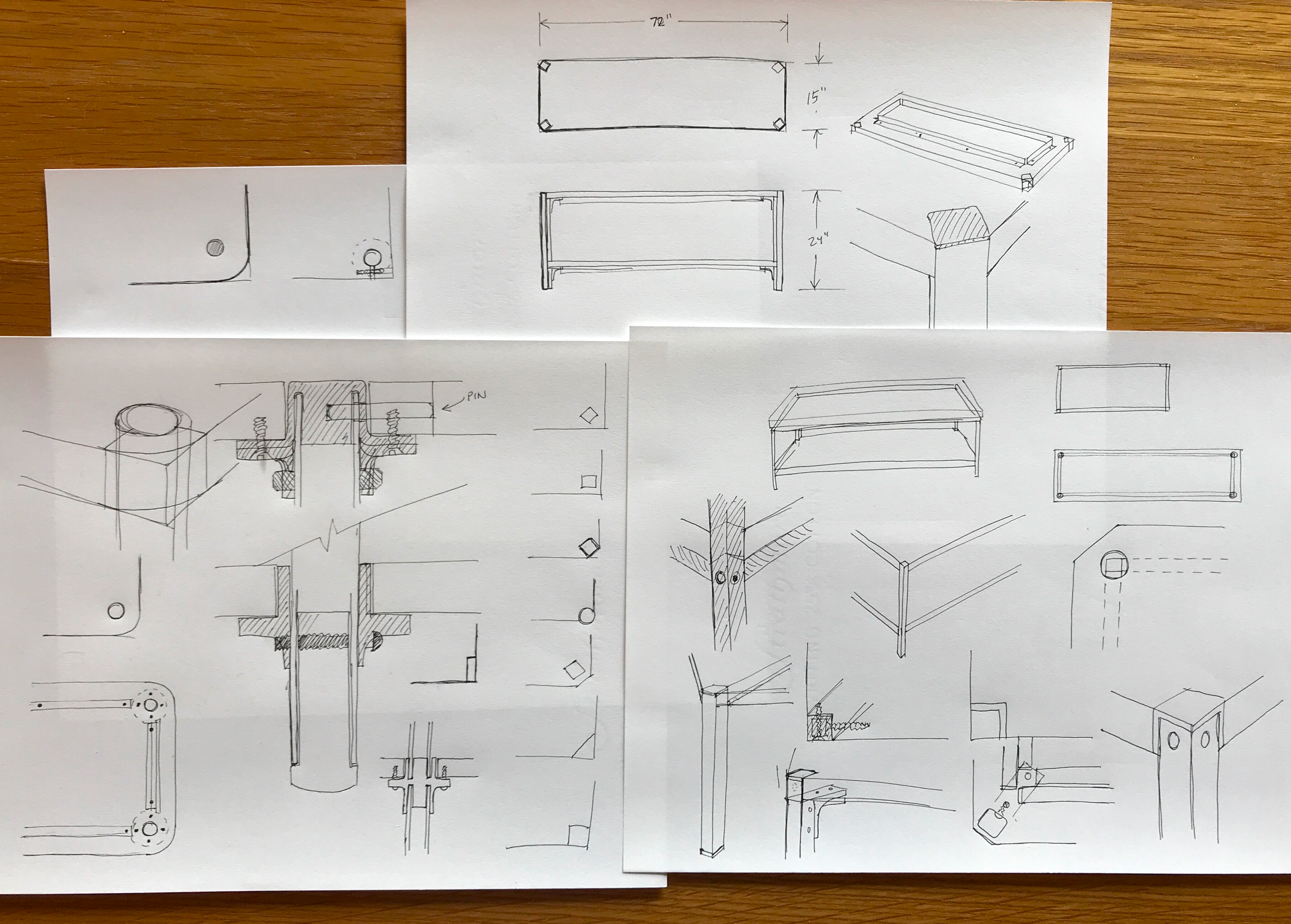

I used anodized aluminum tube for the legs for low weight, strength, slimness, and a nice color/finish contrast to the wood. I used ¾” birch plywood, which is on the thin side, for the ~6-foot span between legs. To help improve stiffness and lend a unique and lightweight visual, I offset the rear legs away from the corners towards the center of the shelf to reduce the span distance. I also attached aluminum U-channel extrusions to the underside of the plywood between the rear feet. This added stiffness while keeping the extrusions out of sight and out of the way of tall items.
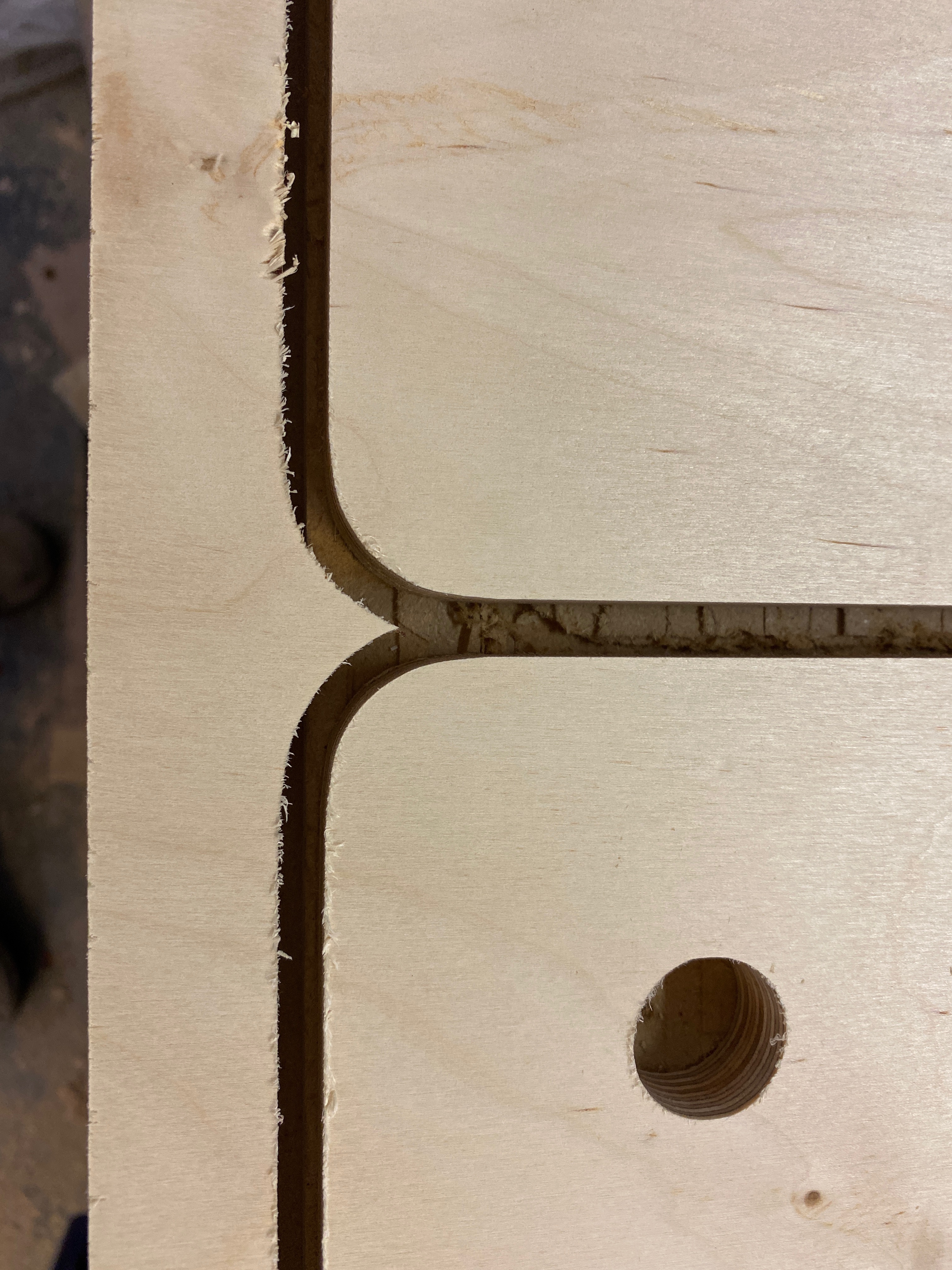
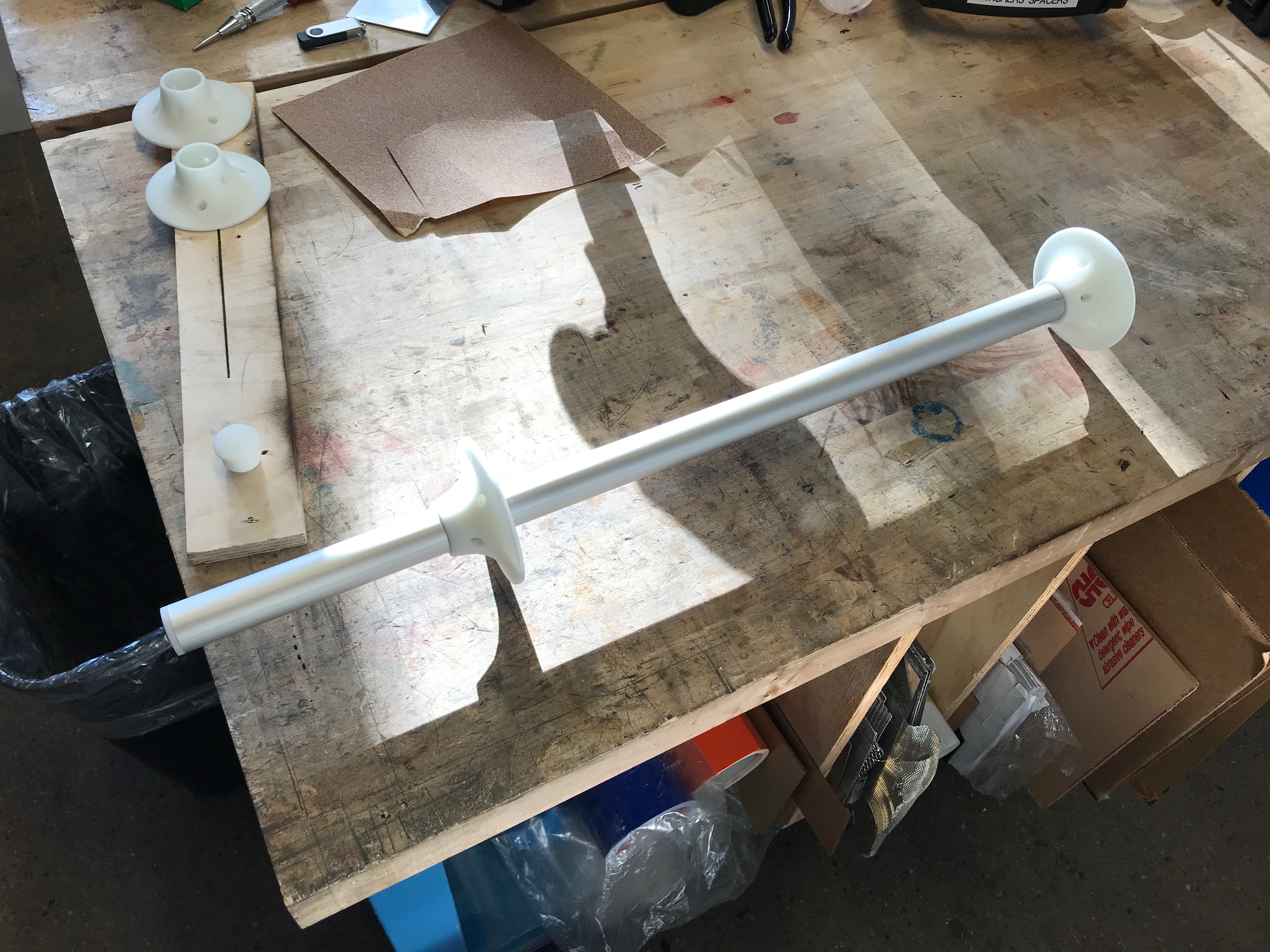
I used 3D-printed joints for strong attachment and to simplify the geometry of the legs and the wood. The joints were printed using a glass-filled SLA resin (Formlabs Rigid resin) that has high stiffness and great strength for geometries without significant stress concentrations. Each joint is attached both to the leg and the shelf surface using three screws. Printed feet with a gently domed surface cap the aluminum legs to provide a slick and smooth face to contact the floor.

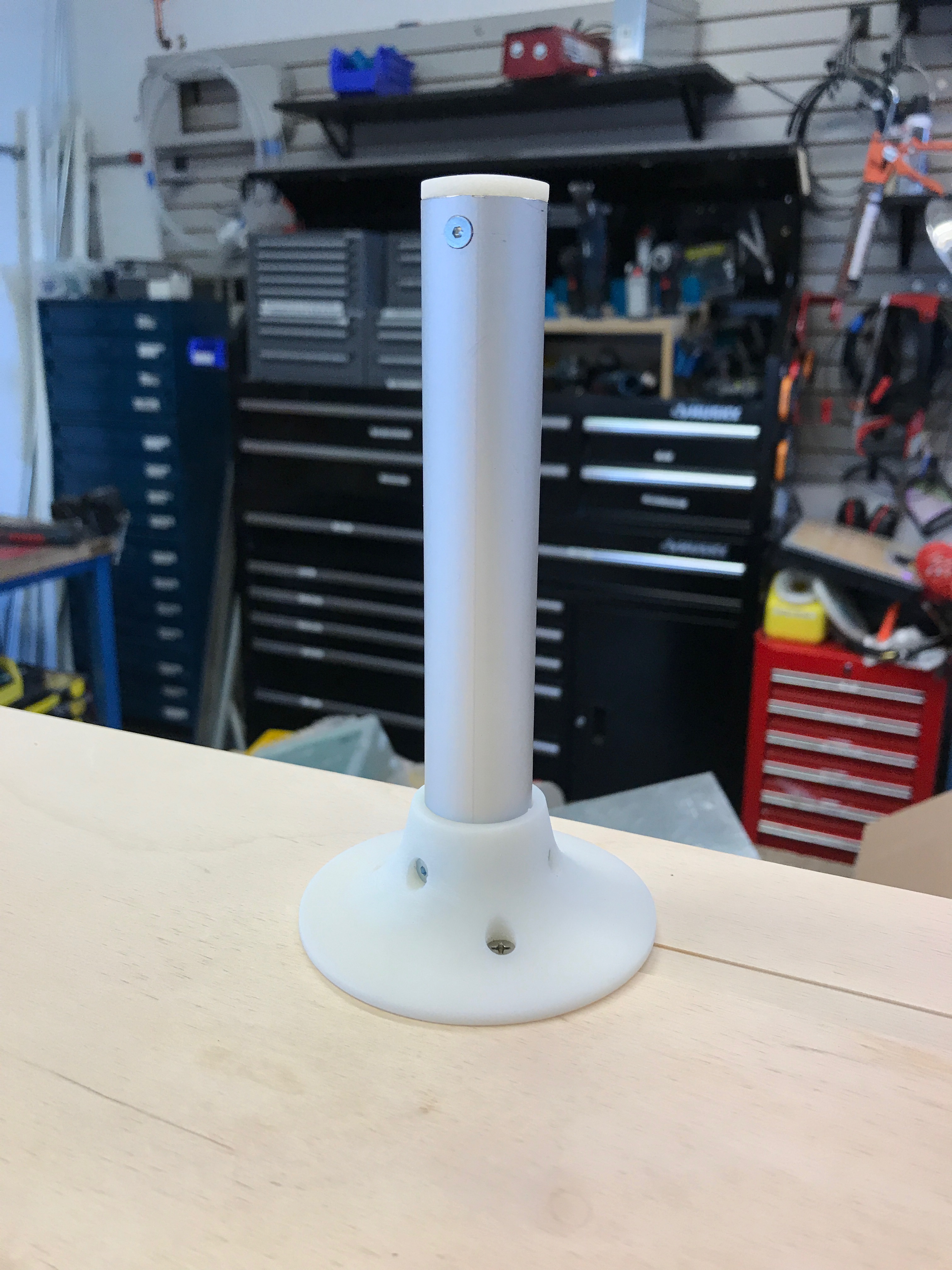
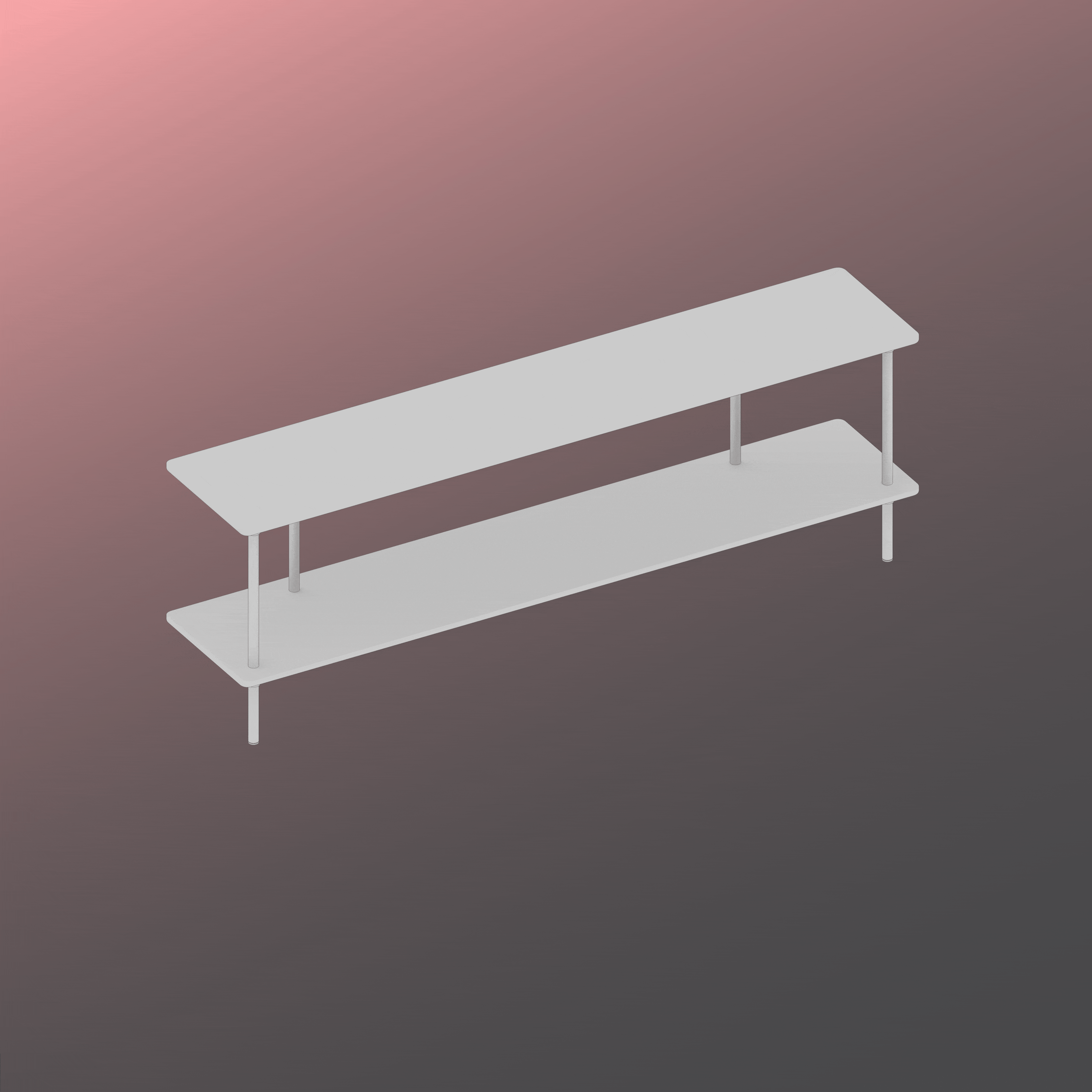
I fabricated three of these shelves for my apartment and the cost of the wood, legs, and finishing materials came to approximately $100 per shelf.

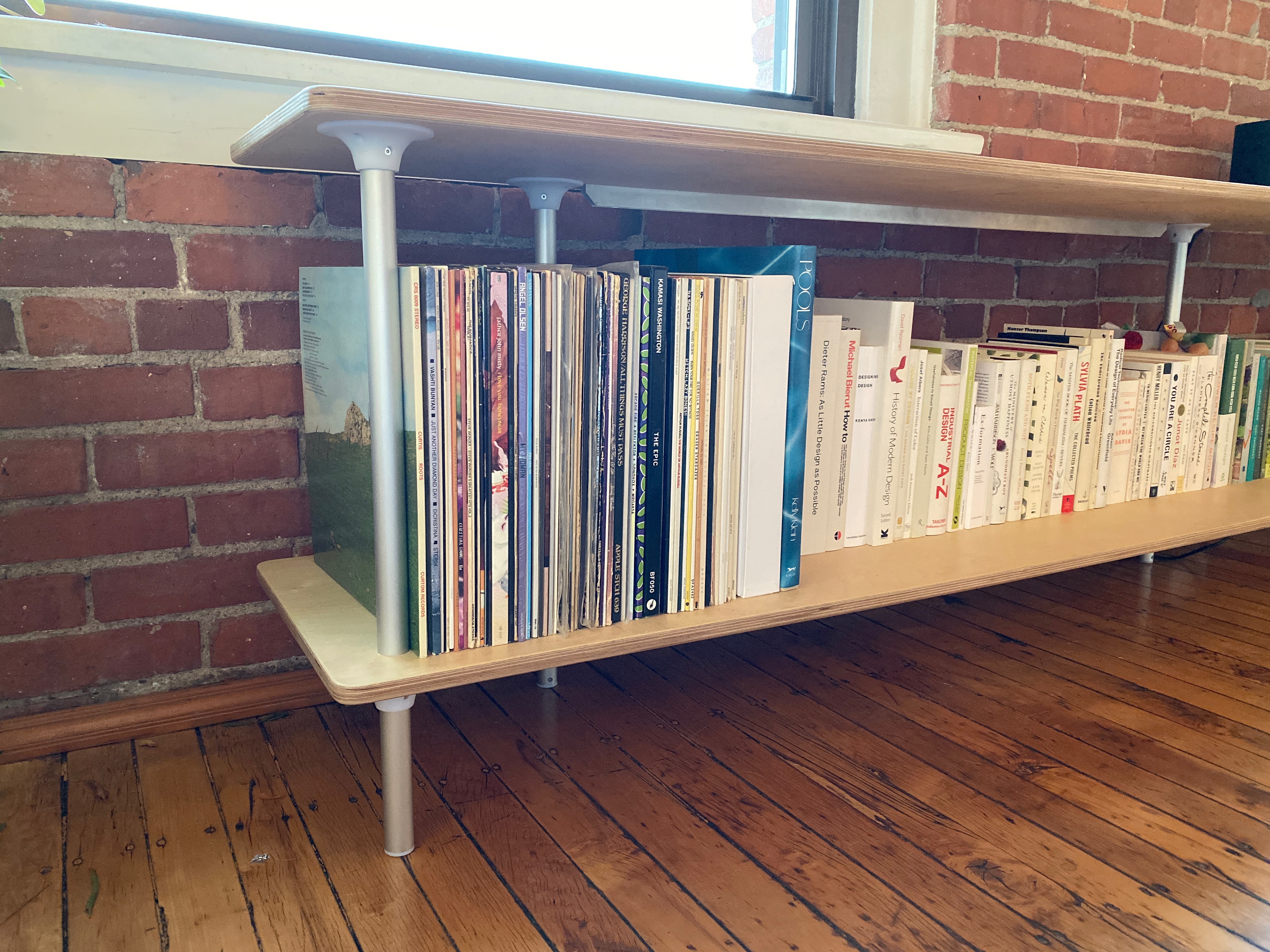
