I work to create enduring products that serve people.

Form 3L
2020, FormlabsMassive prints with minimal effort
Work
︎ Sketching
︎ Concept development
︎ Prototyping
︎ User testing
︎ DFM
︎ CMF development
︎ Packaging design
︎ Visualization
︎ Design leadership
︎ Collaboration with suppliers and CMs
︎ Cosmetic specification and control
︎ Sketching
︎ Concept development
︎ Prototyping
︎ User testing
︎ DFM
︎ CMF development
︎ Packaging design
︎ Visualization
︎ Design leadership
︎ Collaboration with suppliers and CMs
︎ Cosmetic specification and control
Goals
︎ Easy interactions with machine components
︎ Accessible handling and removal of large parts
︎ High-quality feel
︎ Good fit with Formlabs brand language
︎ Professional yet friendly aesthetic
︎ Easy interactions with machine components
︎ Accessible handling and removal of large parts
︎ High-quality feel
︎ Good fit with Formlabs brand language
︎ Professional yet friendly aesthetic
3D printing size limitations are a clear barrier to prototyping flexibility and speed for designers and engineers. Prototyping large objects with desktop printers involves considerable time and effort to split models in CAD and join individual parts with alignment features, fasteners, adhesives, etc. Printing many small objects for production runs or for dental applications is also currently limited by the number of models that can fit in the build area. The Form 3L was created by scaling up the Form 3 technology to address these limitations. I led the industrial design work for Form 3L and focused on making this new workflow (with large, heavy resin prints) accessible for as wide a group of users as possible.
The Form 3L design foregrounds the two most important interaction surfaces on the product: the cover and the display. The coplanar orange plastic window and the display glass stand apart as glossy sharp surfaces among a background of matte grey tones. The profile cut from side to side reinforces this emphasis while simultaneously creating access for the cover handle and a subtle location for a front-facing speaker. The cover handle is made from an extruded aluminum profile containing finger ledges for comfortable closing and opening, and the angled front face improves the ergonomics of both screen and cover interactions. The protrusion in the rear profile of the body visually echoes the front profile while creating space for internal components without increasing overall machine depth.


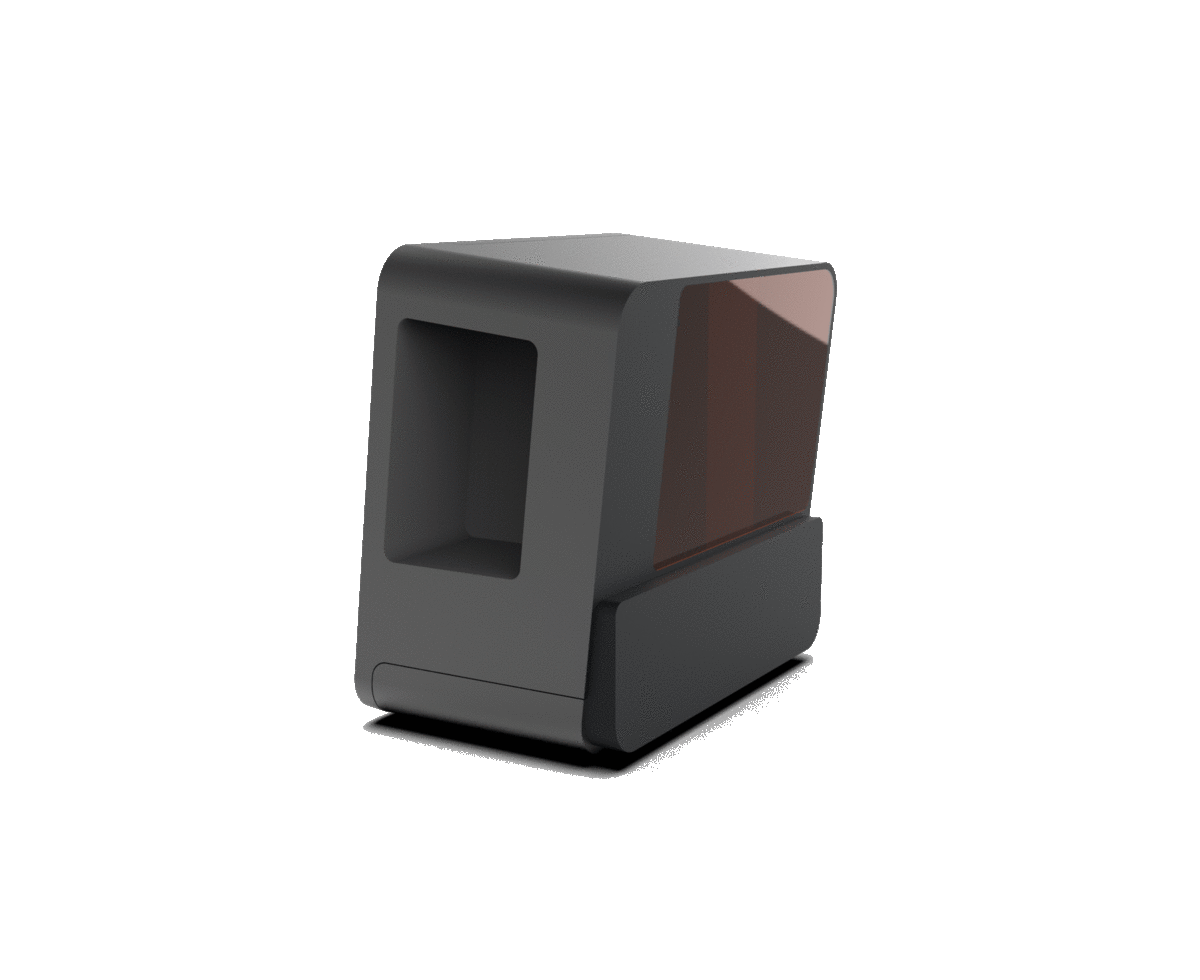


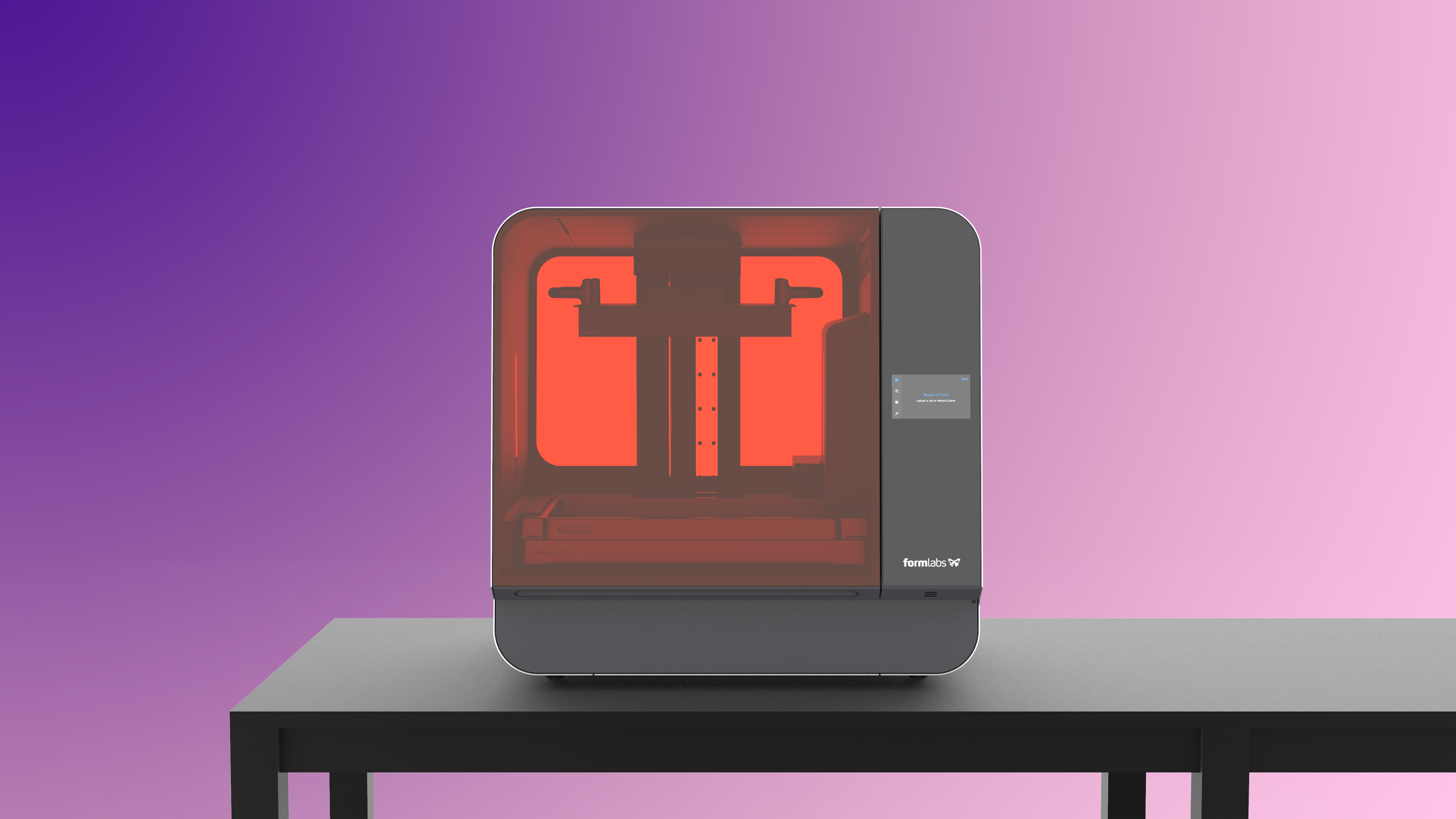
The parts are printed on the build platform and are transported between machines and washed while still attached. As such, the build platform is designed to accommodate easy and comfortable handling and transport of large and resin-covered parts. The handles extend beyond the sides of the aluminum body to allow the assembly to be easily flipped upside down after printing without resin spills. This handle geometry also helps shorter people reach the handles in the machine from below without interference from the platform.

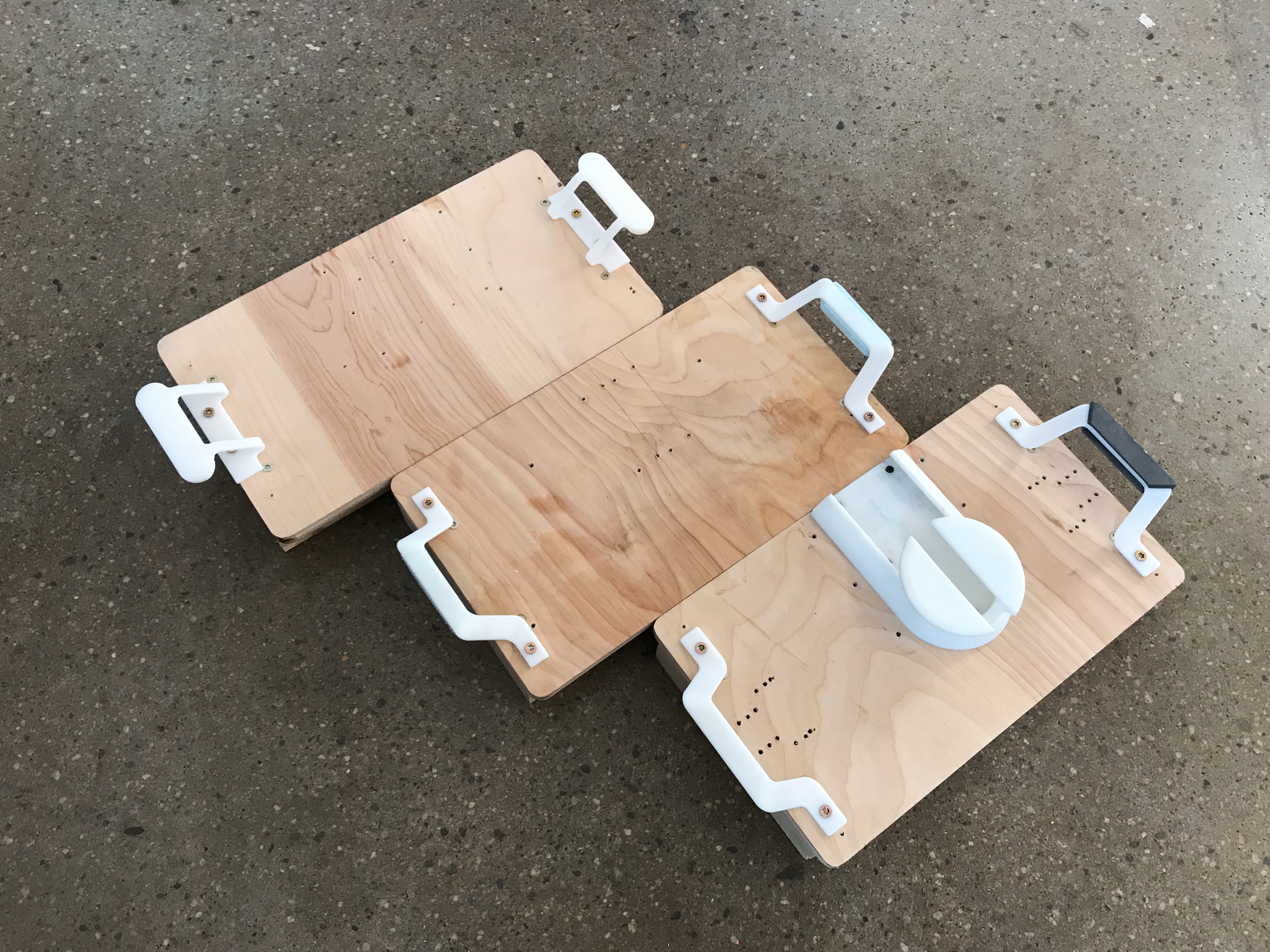
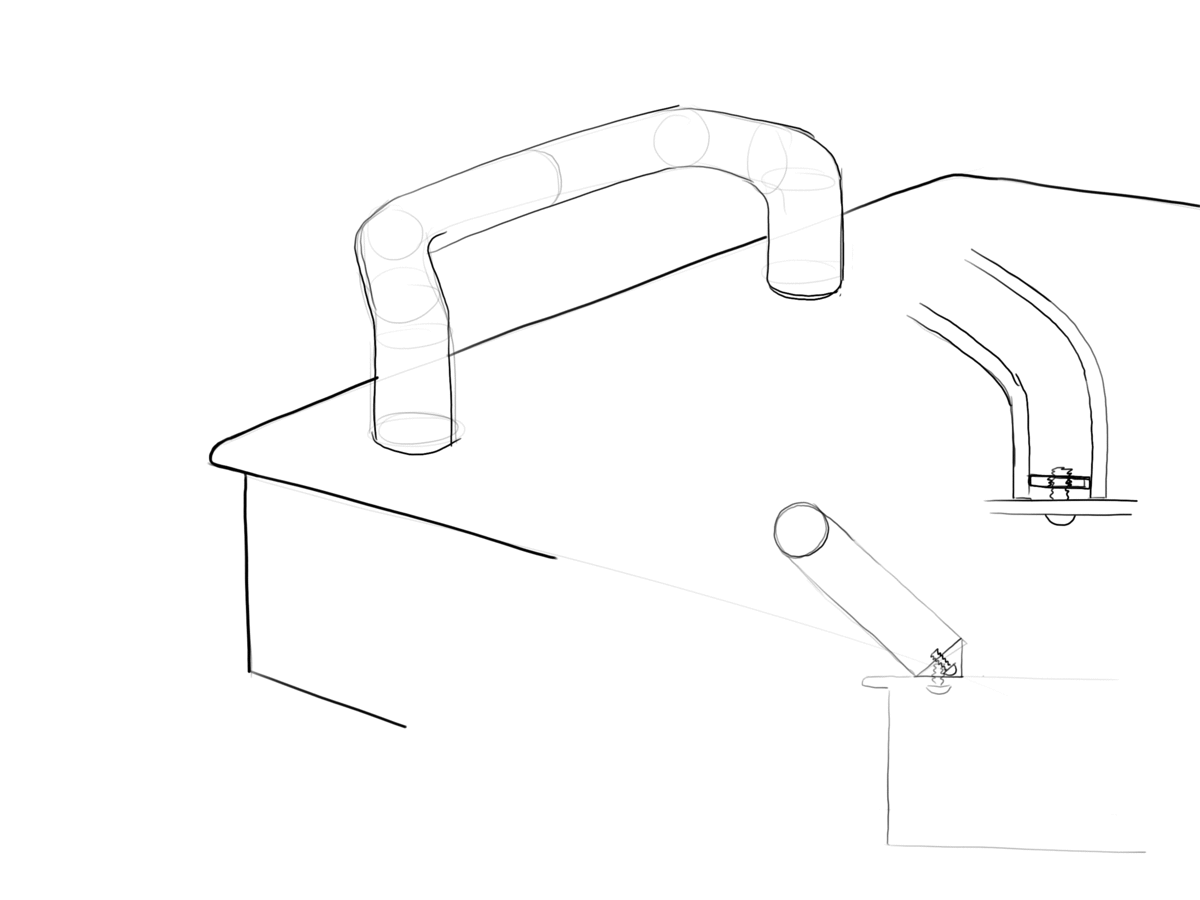
The post features in the handles create two key usability benefits: 1) They maintain space for finger access between the handle surface and the table when the platform is resting upside down, and 2) they allow the platform to lock against the side of a table in multiple orientations to resist the high forces exerted during the part-removal process. In order to achieve a comfortable 17mm-diameter handle, we worked with the molder to create a solid polypropylene part with minimal sink and molding issues.

The consistency of form between the platform and the carriage clearly shows the intended insertion location, as the actual mating geometry is hidden from view. The latch to lock the build platform back into place is a machined piece of aluminum that echoes the rounded form of the handles and is coated in the same color. A blue marker underneath the latch signifies that it needs to be closed to properly secure the platform.


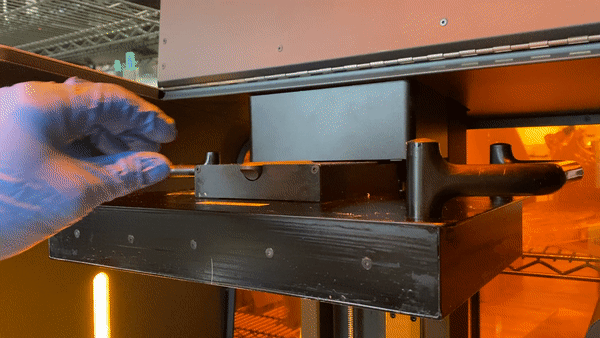
Watching a part take shape is an exciting part of the printing process and good part visibility during printing is an important feature for diagnosing possible print errors. For these reasons, we designed lighting modules to illuminate the interior chamber during printing. The resin is cured using UV light so we used narrow bandwidth yellow/orange LEDs to ensure that the lights don’t inadvertently cure the resin. We also programmed these lights to provide notification pulses when user attention is required.







