I work to create enduring products that serve people.

Form 3
2019, FormlabsBringing simplicity and accessibility to a complex and powerful tool
Work
︎ Sketching
︎ Concept development
︎ Prototyping
︎ User testing
︎ DFM
︎ CMF development
︎ Visualization
︎ Design leadership
︎ Collaboration with suppliers and CMs
︎ Cosmetic specification and control
︎ Sketching
︎ Concept development
︎ Prototyping
︎ User testing
︎ DFM
︎ CMF development
︎ Visualization
︎ Design leadership
︎ Collaboration with suppliers and CMs
︎ Cosmetic specification and control
Goals
︎ Improve ergonomics
︎ Space efficiency
︎ Improve repairability and longevity
︎ Reduce cost
︎ Solve Form 2 problems (cracking covers, tank management)
︎ Improve ergonomics
︎ Space efficiency
︎ Improve repairability and longevity
︎ Reduce cost
︎ Solve Form 2 problems (cracking covers, tank management)
The Form 3 introduced a new 3D printing process for better print quality and reliability. I led the industrial design of the Form 3 with the goals of creating a highly accessible hardware experience, evolving the Formlabs design language, and resolving a number of issues with the existing product ecosystem.

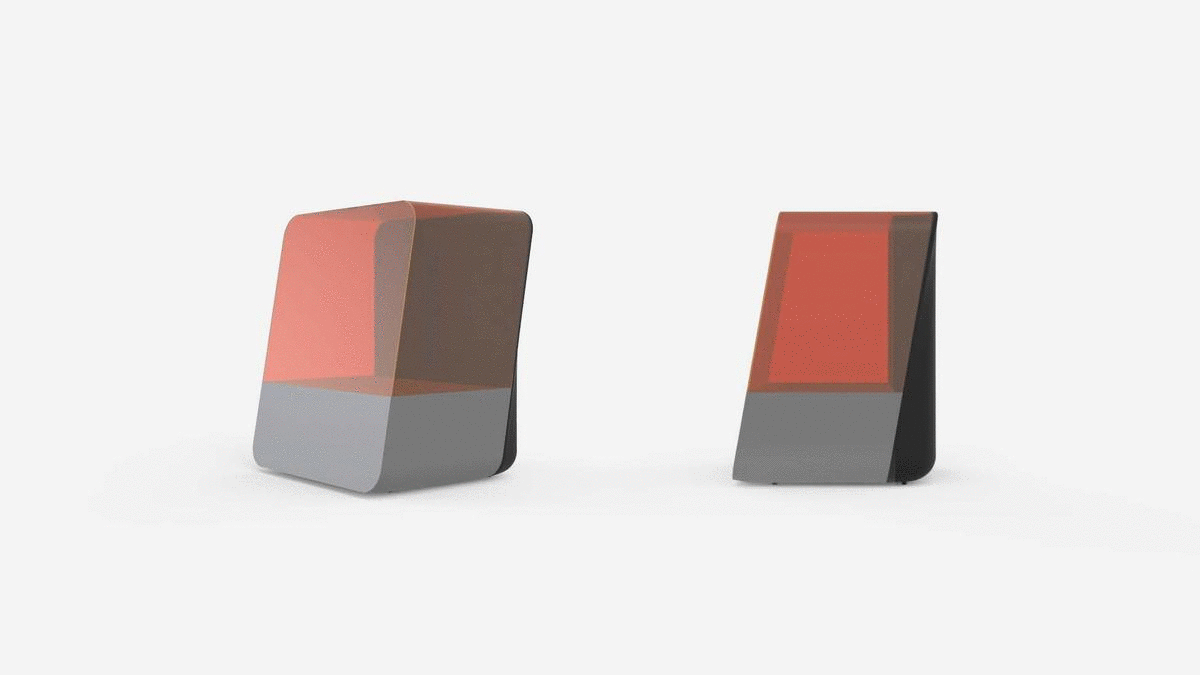
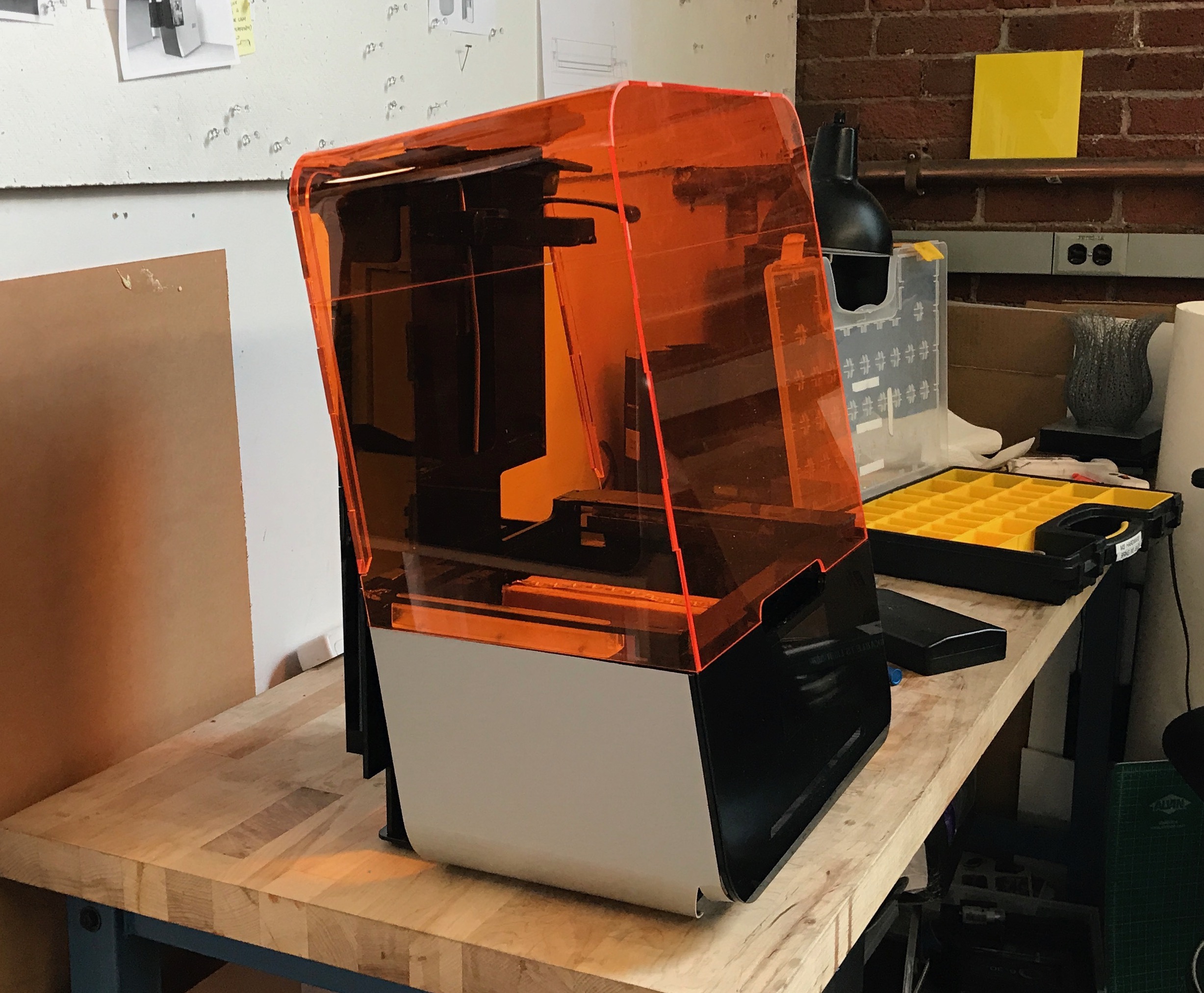
The Form 3 design features a gently tilted front face, which creates continuous and comfortable part viewing and interaction surfaces. A recessed slot is subtracted symmetrically across the part split to form handle geometry for opening and closing the cover. The tilt of the body also reduces cover depth, which in turn reduces the total height of the product when open, enabling a greater variety of use locations. The hinge and IO recess were designed to allow use of the printer flush against a wall, which maximizes the usable work surface in front of the machine for components like tanks or build platforms.



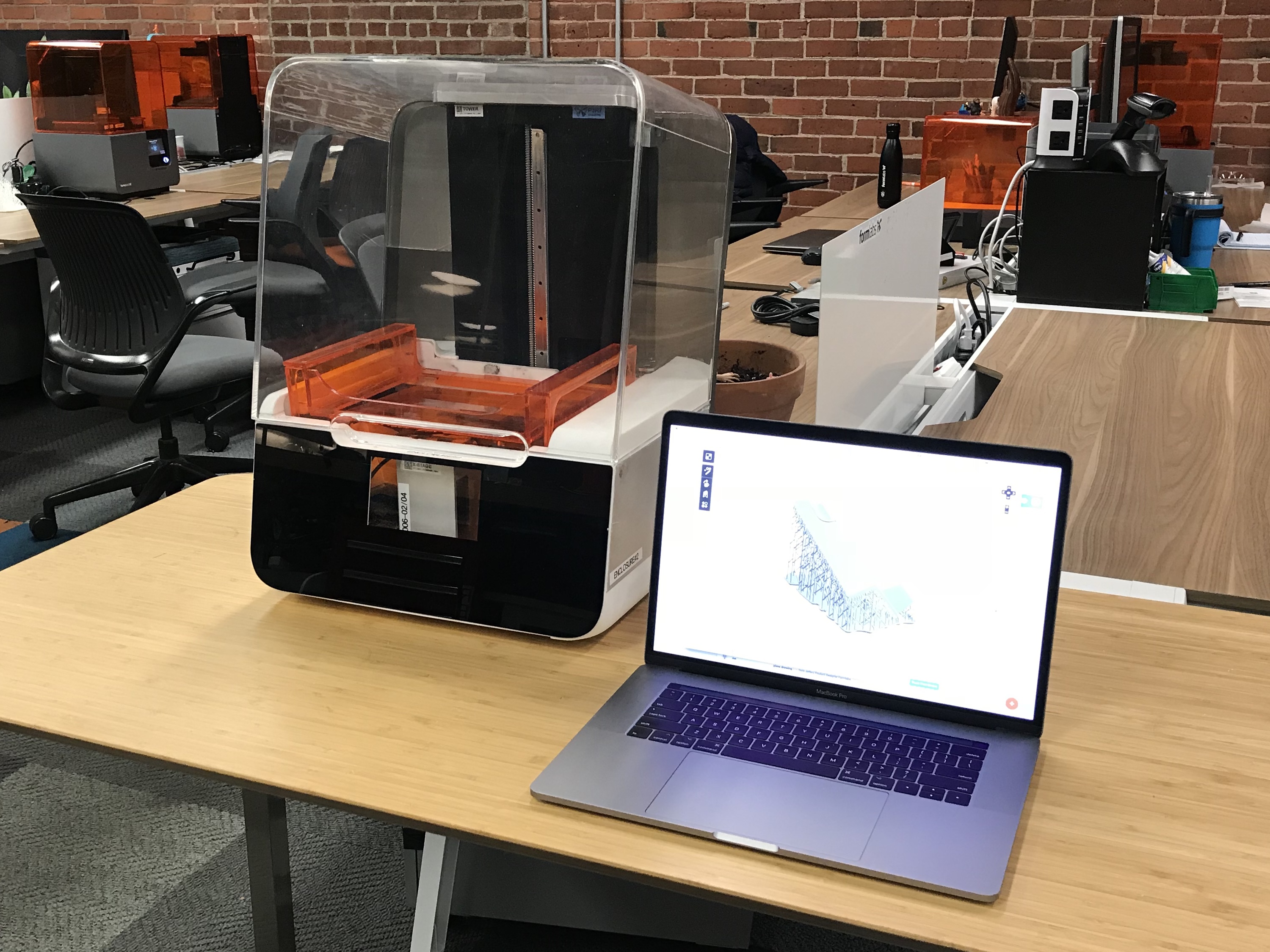
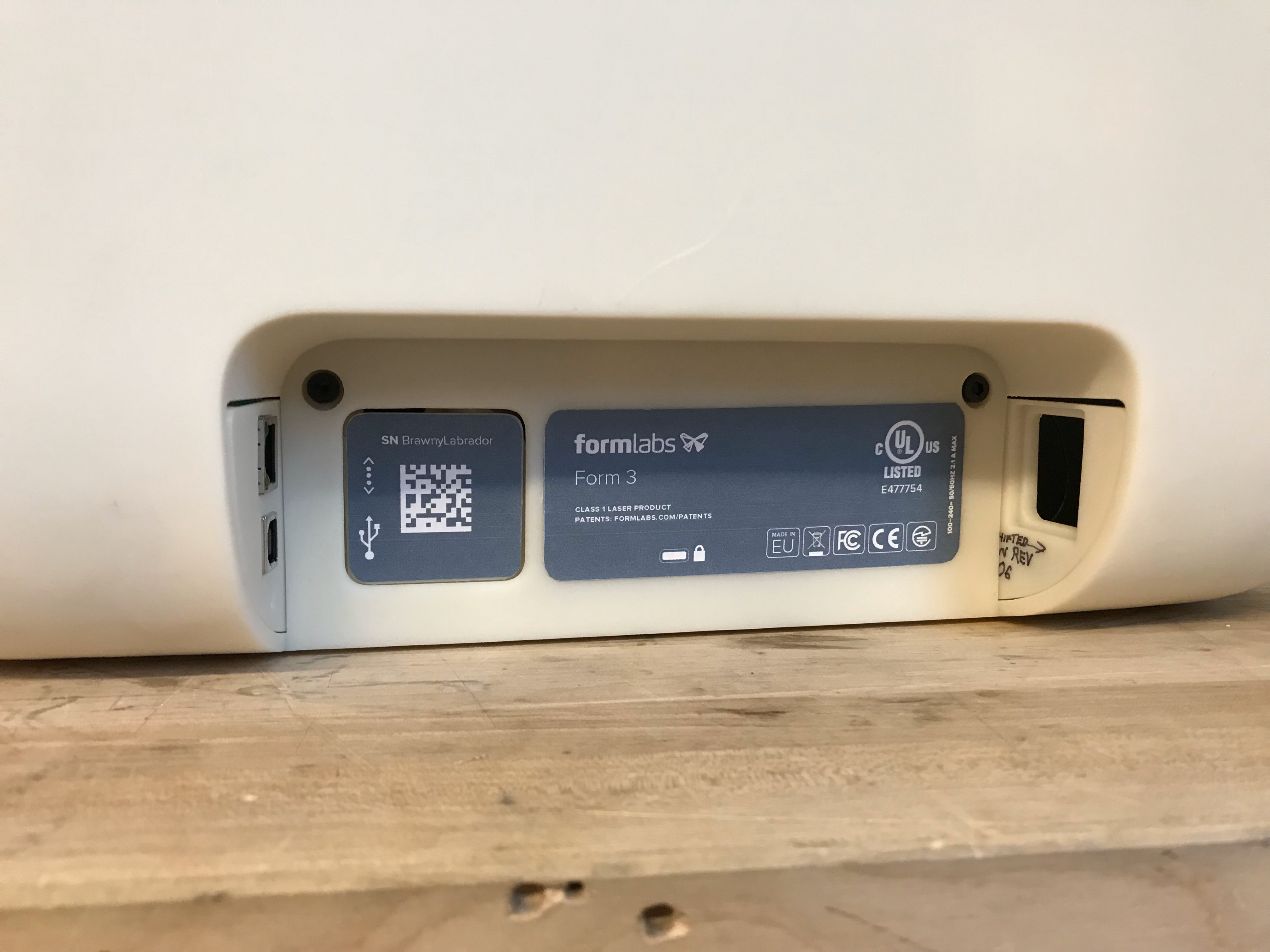

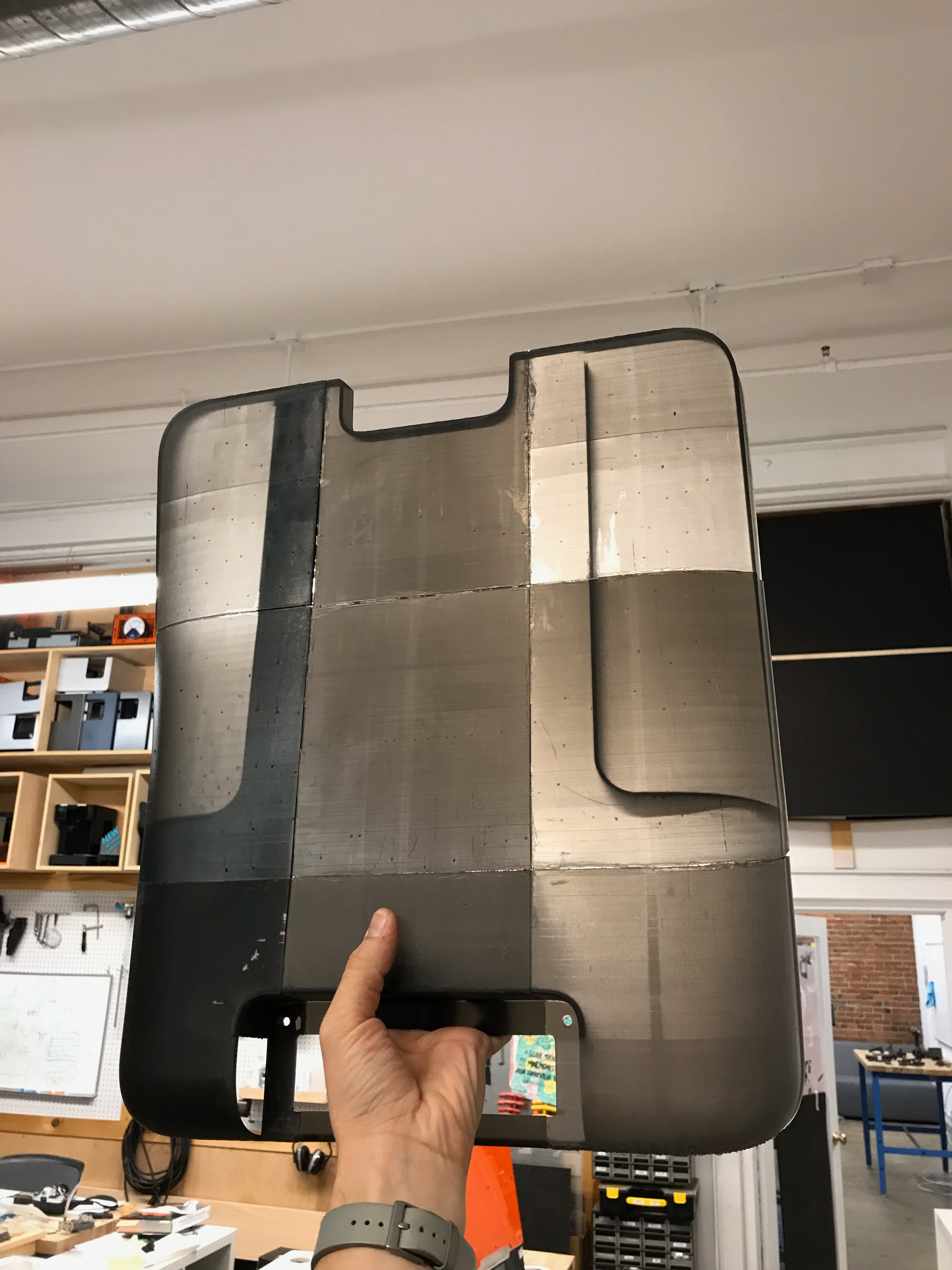


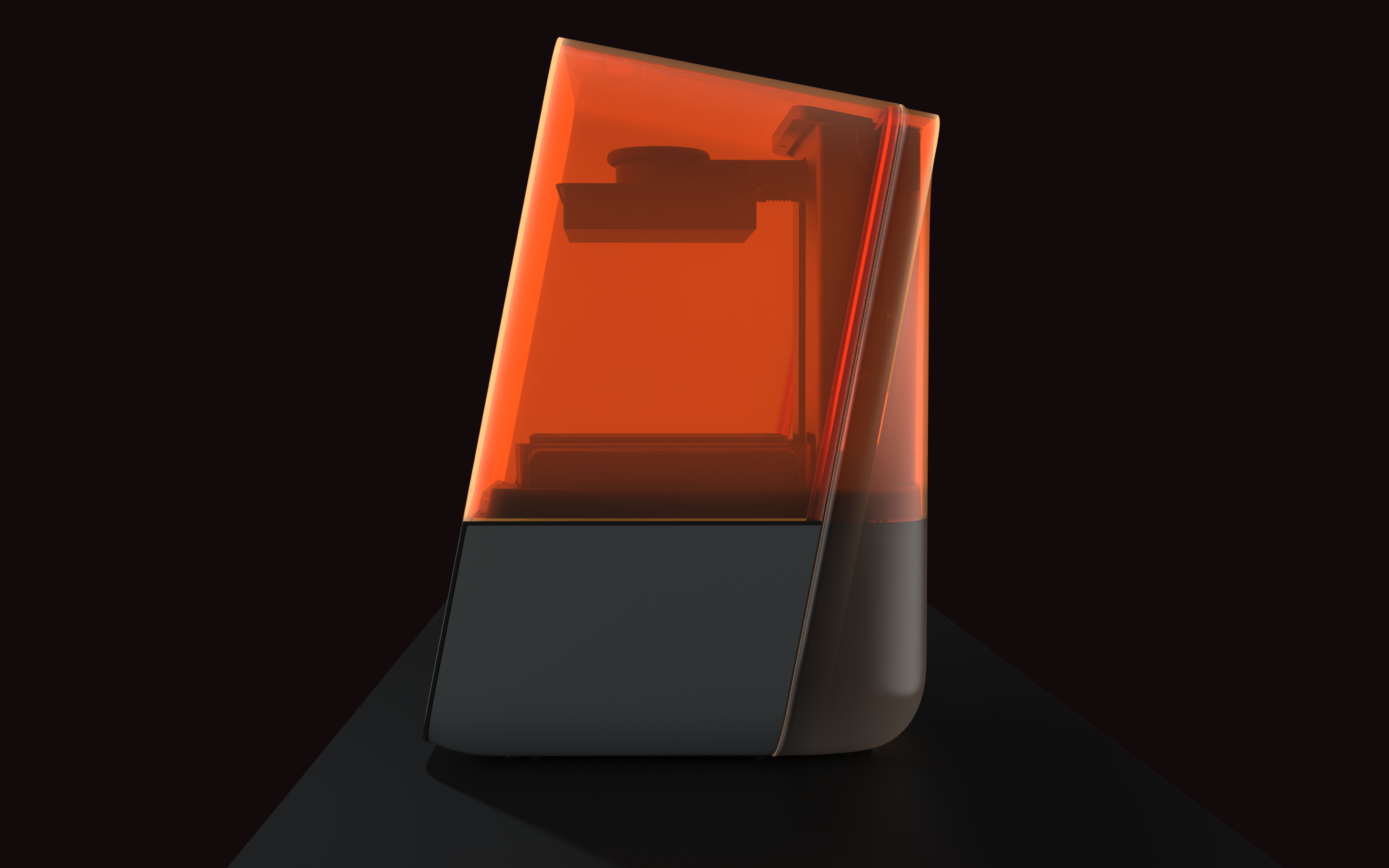
The design also features an oversized glass display that reduces gaps and allows for better cleanability in case of resin drips when removing a fresh print. The materials across this resin-based printer were selected for robust chemical resistance and the forms were developed with sufficiently large internal radii for easy cleanability. The construction and part split approaches were developed to eliminate any upward-facing gaps that could trap liquid resin.
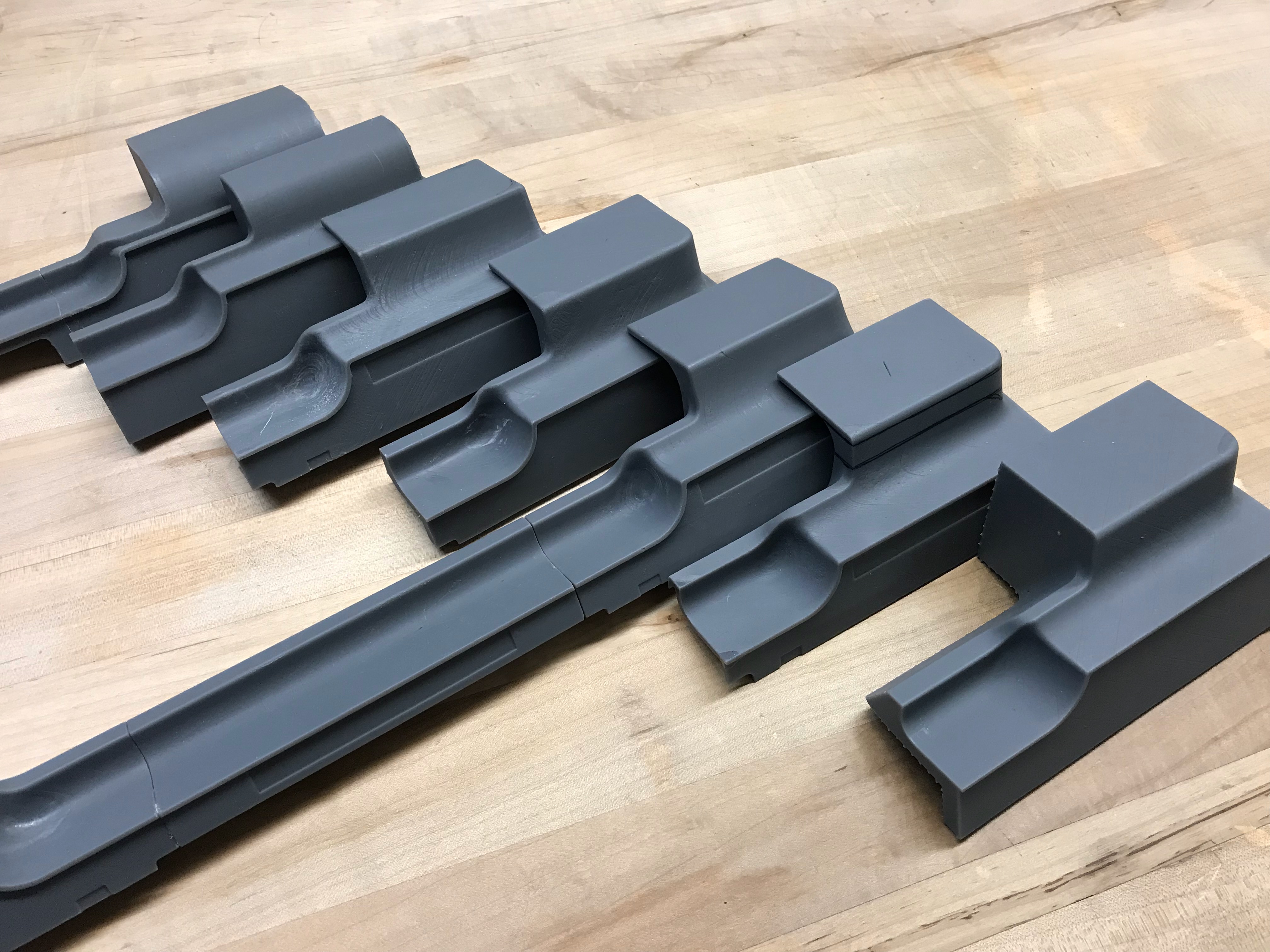
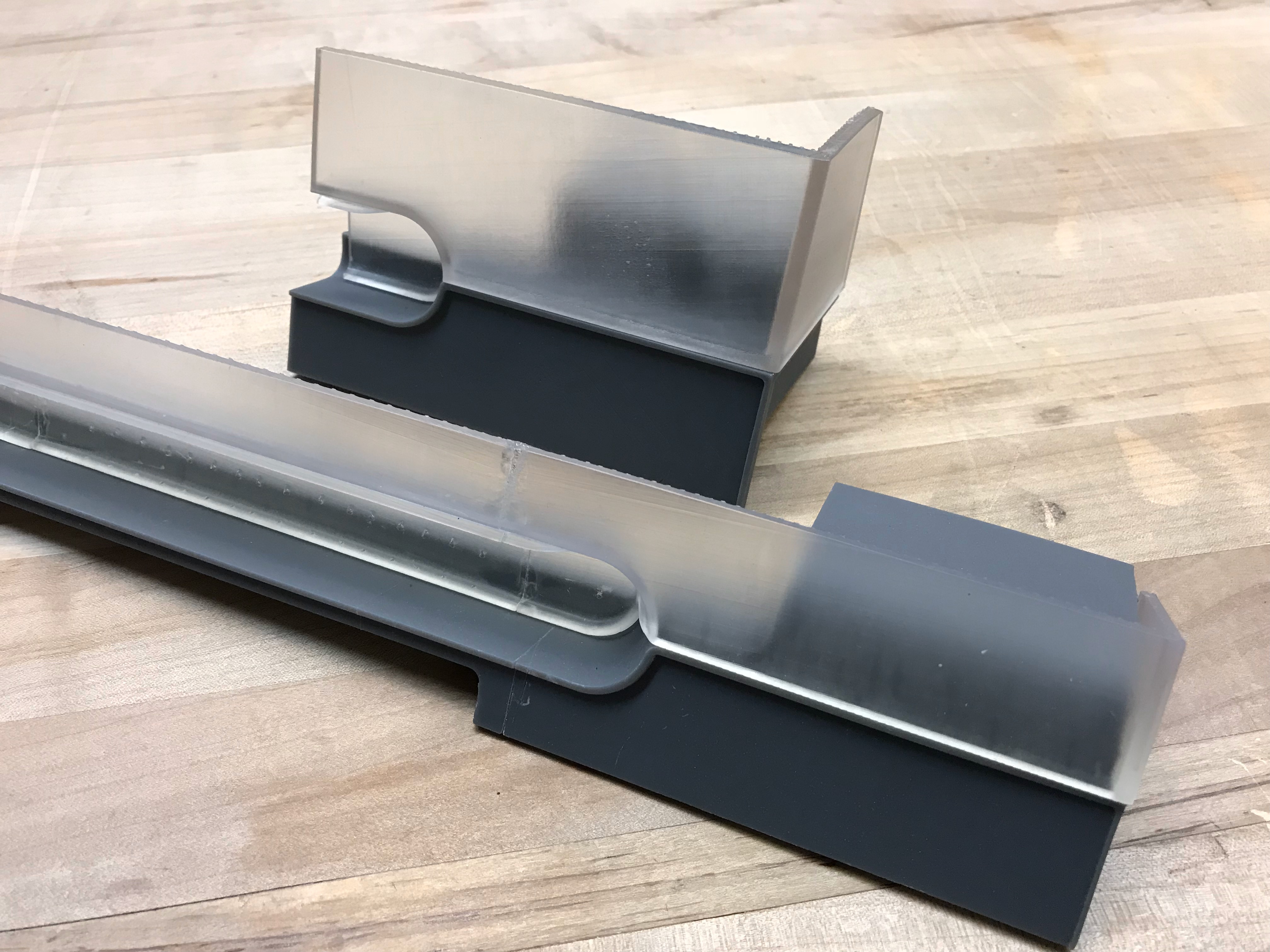

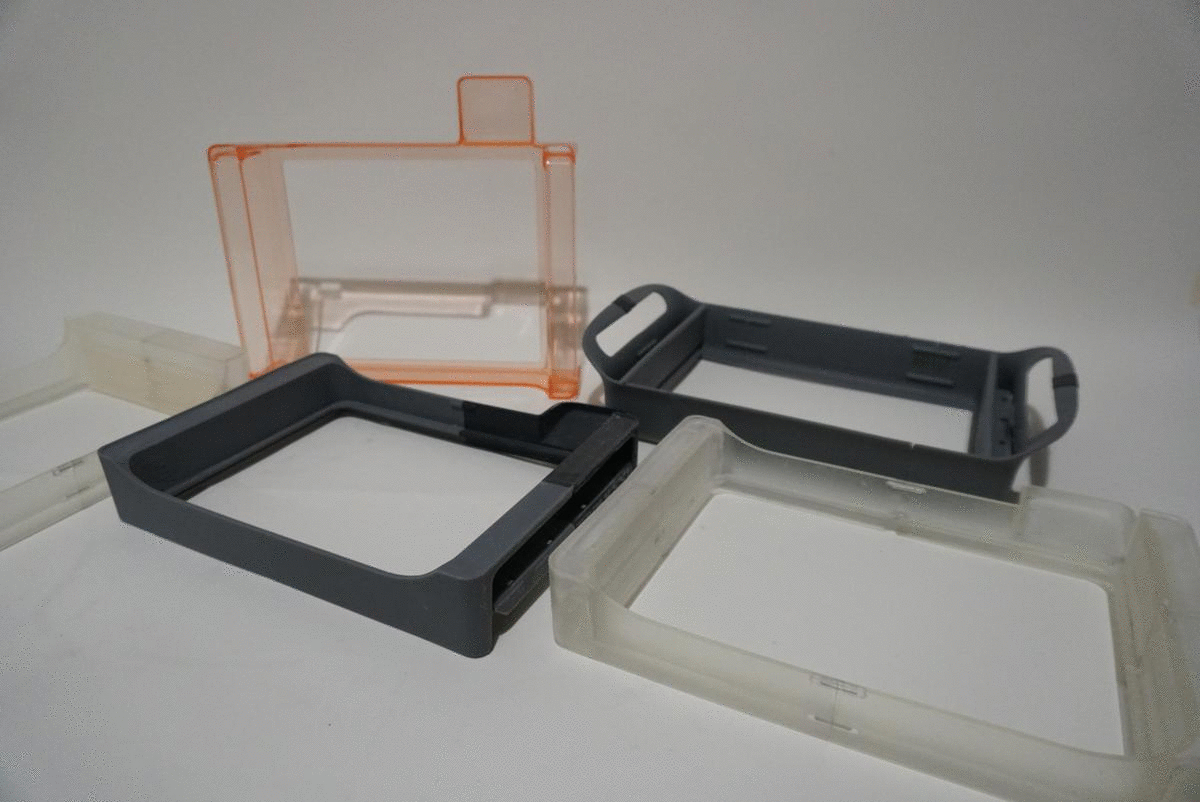
The cover used in the previous product often cracked after exposure to resin. To remedy this, we designed the new, larger, transparent orange cover with improved moldability and chemical resistance to reduce cost and field failures. For this part, I handled the mechanical engineering and material selection and worked with the supplier to develop the molding approach and tool design. While this was originally viewed as a highly risky part, the final manufacturability of the design was very successful.


The previous resin tanks were difficult to handle and store, which resulted in longevity issues. The new tank design featured a flexible film that introduced new durability concerns and mechanical complexity. To solve these issues, I developed a tank design with improved handle ergonomics and insertion UX that hides much of the added complexity. I also designed a case to extend the product life by protecting the film from damage and preventing UV light exposure and premature resin curing. This case also features integral carrying handle recesses and alignment features for easy stacking and efficient storage.




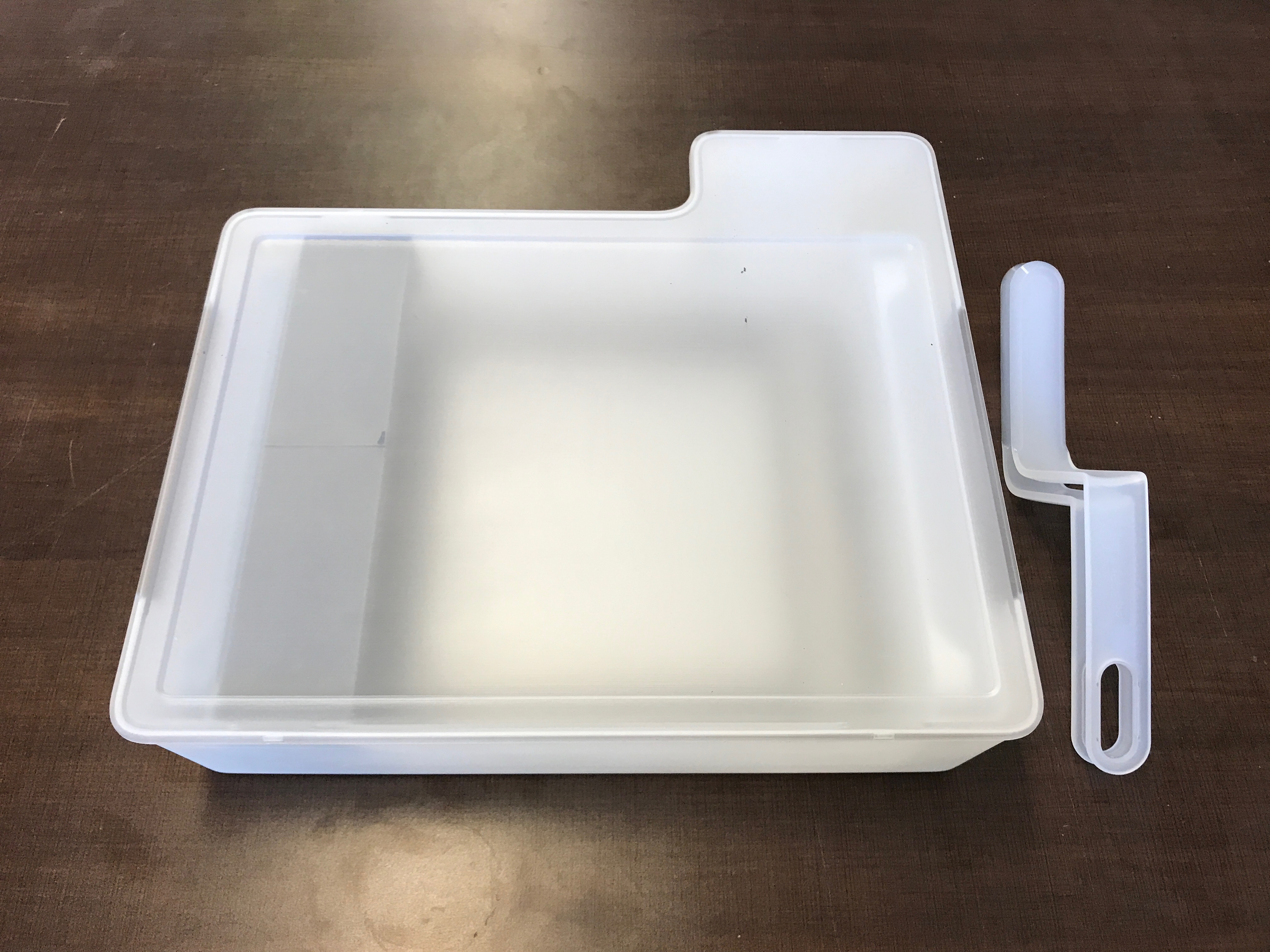
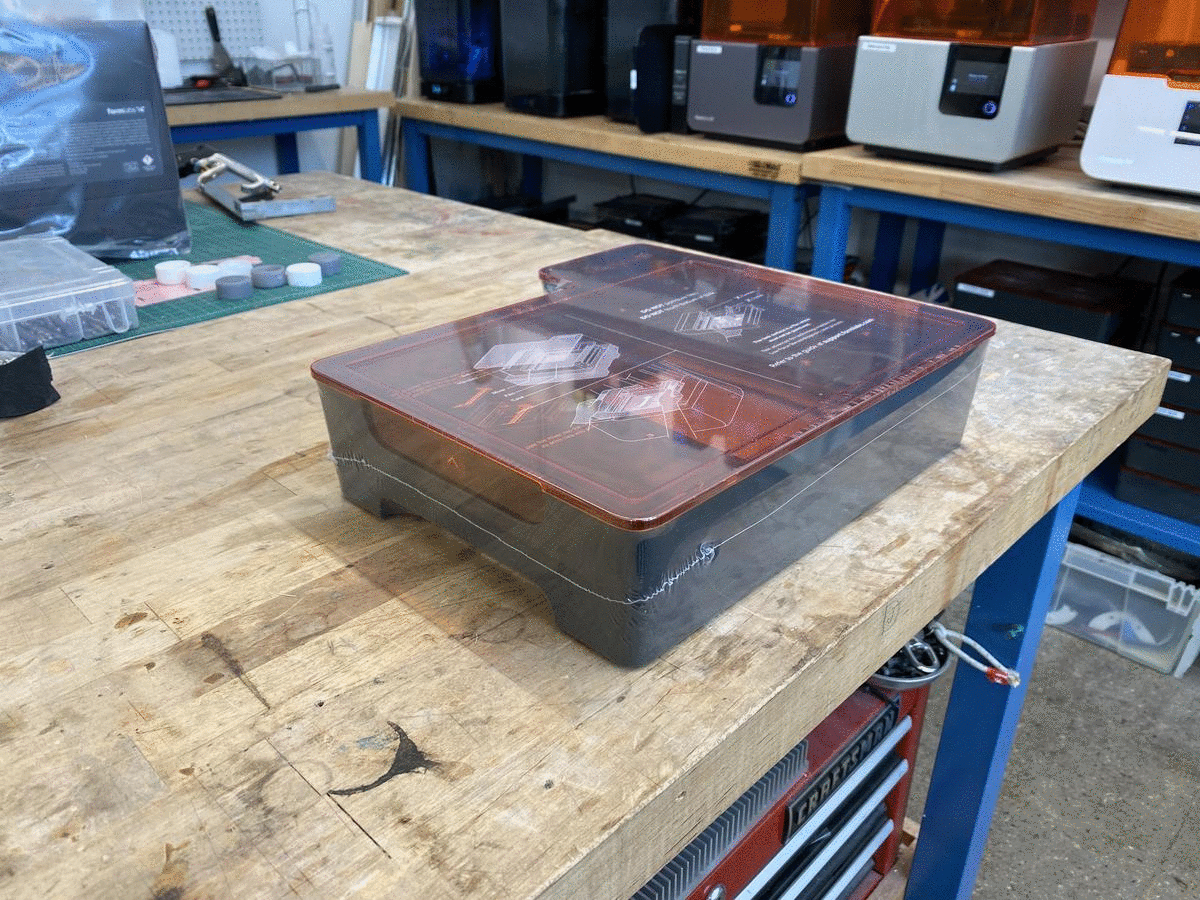
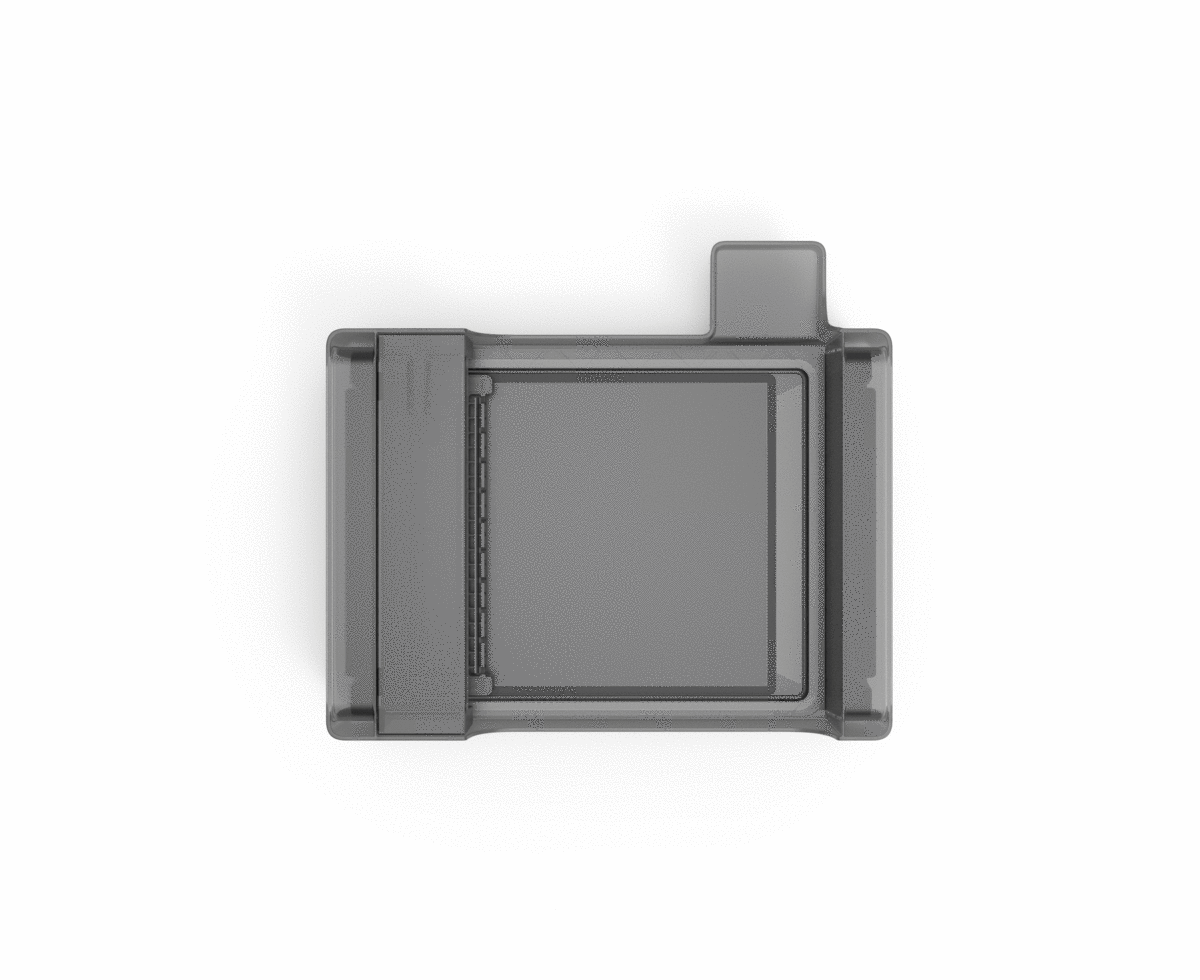
Unnoticed errors can result in a significant loss of printing time. In order to prevent these kinds of scenarios, I developed a lighting feedback system to visually alert users in the event of an error. I designed a light module at the top of the product that is visible from the rear and sides of the machine, while the front features an illuminated Formlabs logo visible through the display glass. During error states, both of these lights pulse to alert users with nearly omnidirectional visibility. The lights take some inspiration from the stack lights used in industrial settings.
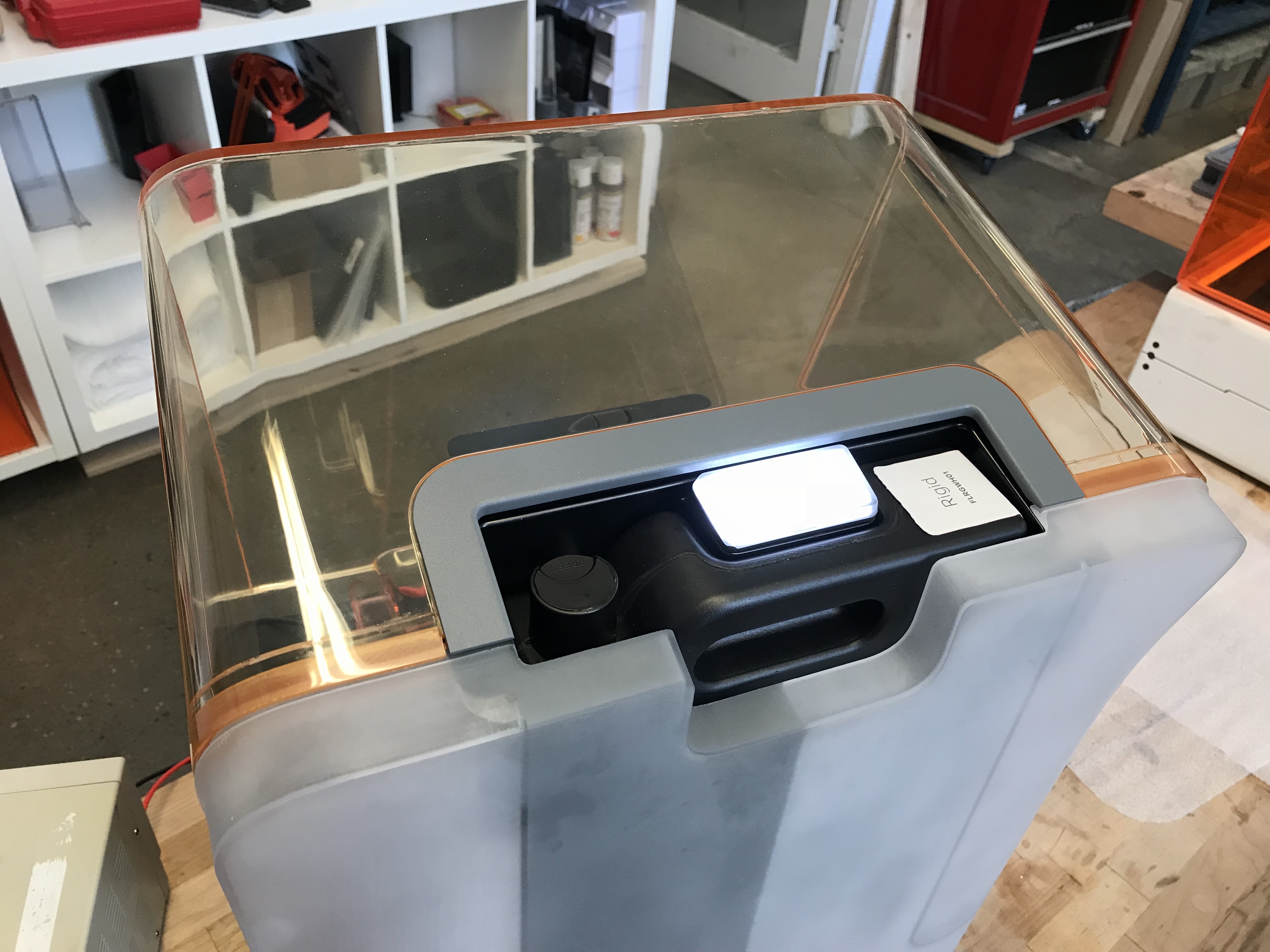
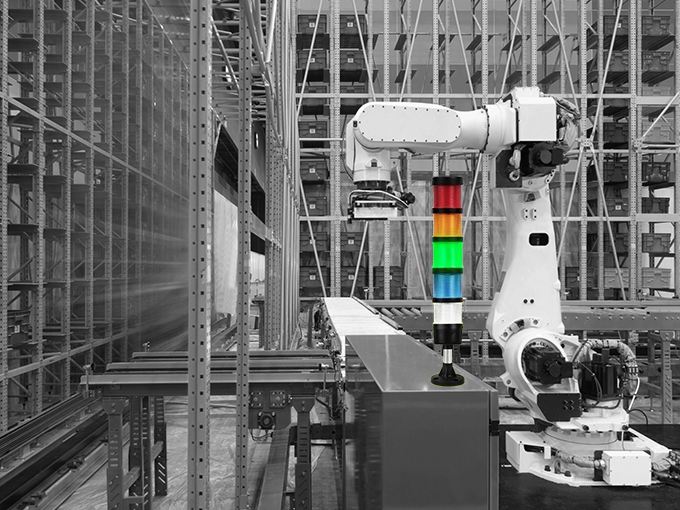
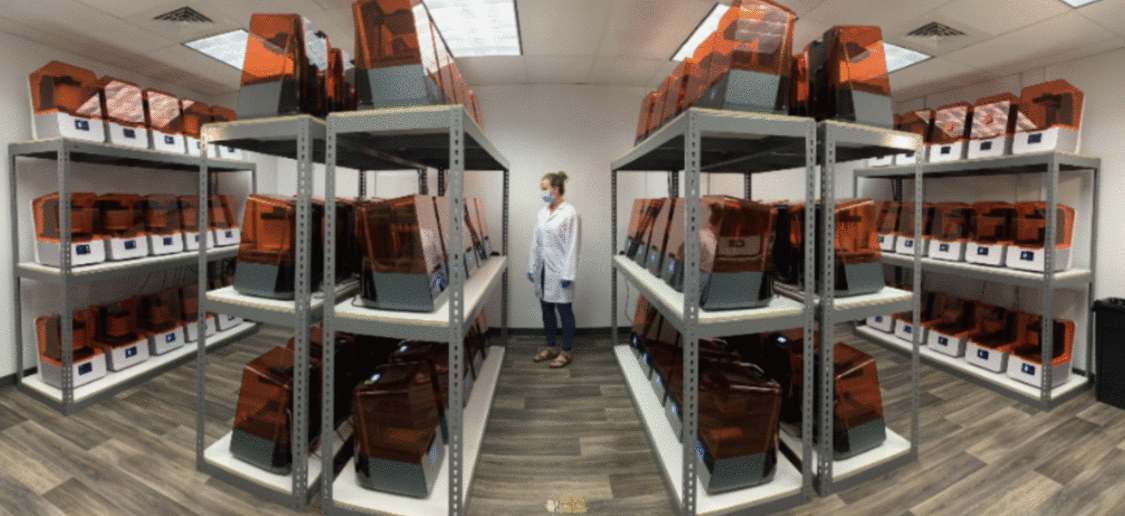
After the launch of the Form 3, I developed a new CMF approach for the Form 3B, a variant of the Form 3 that is aimed at the dental market.

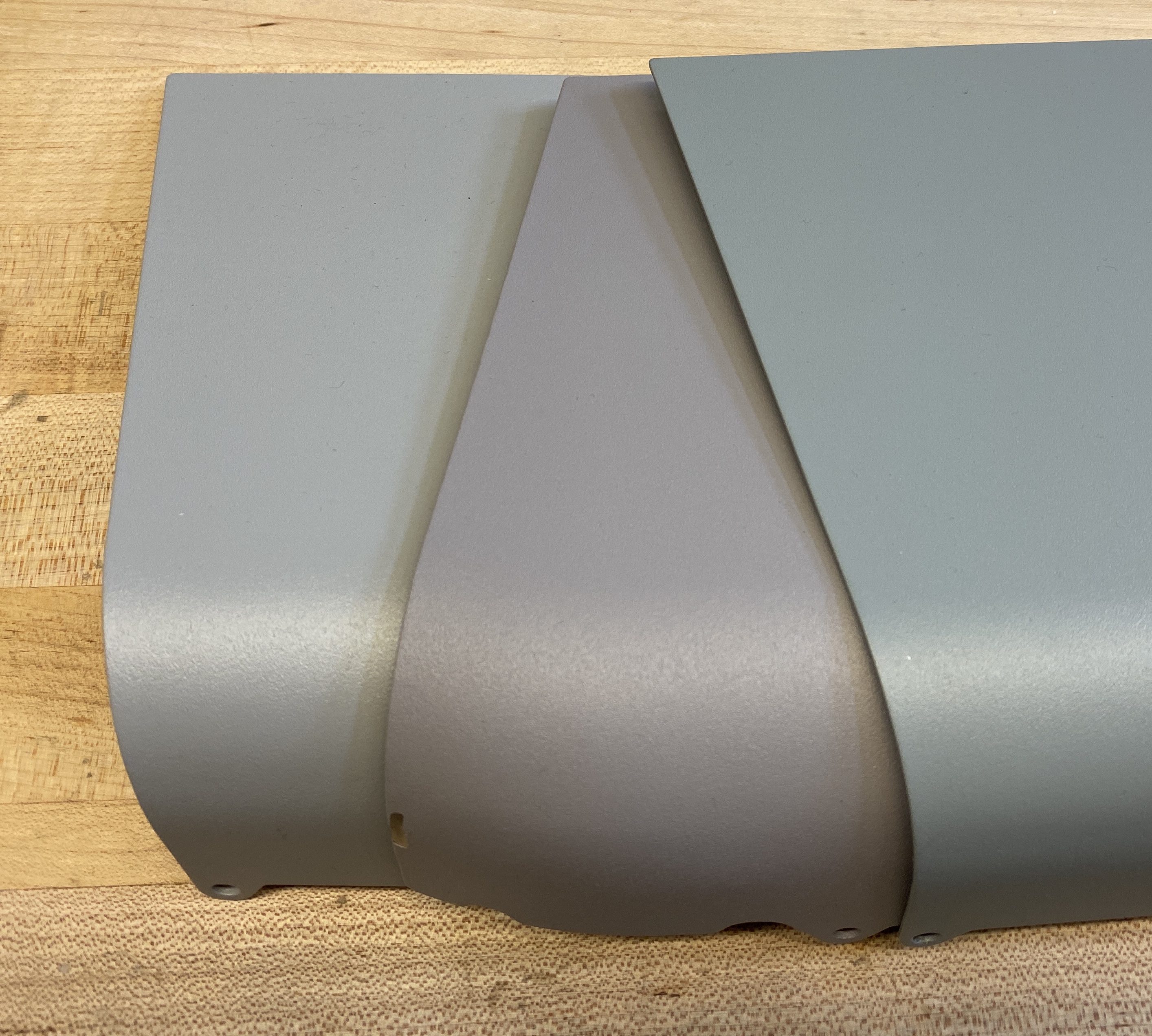
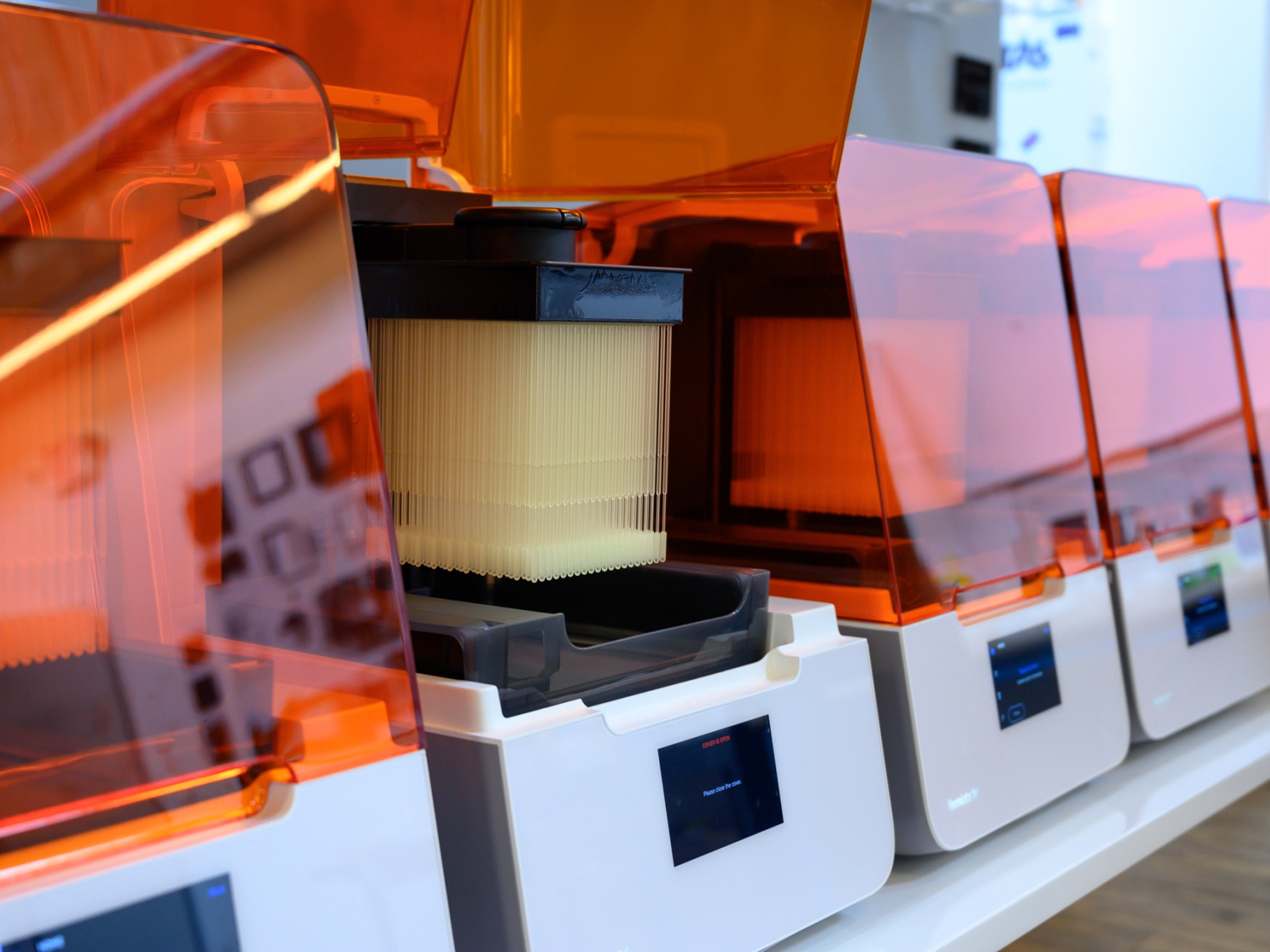
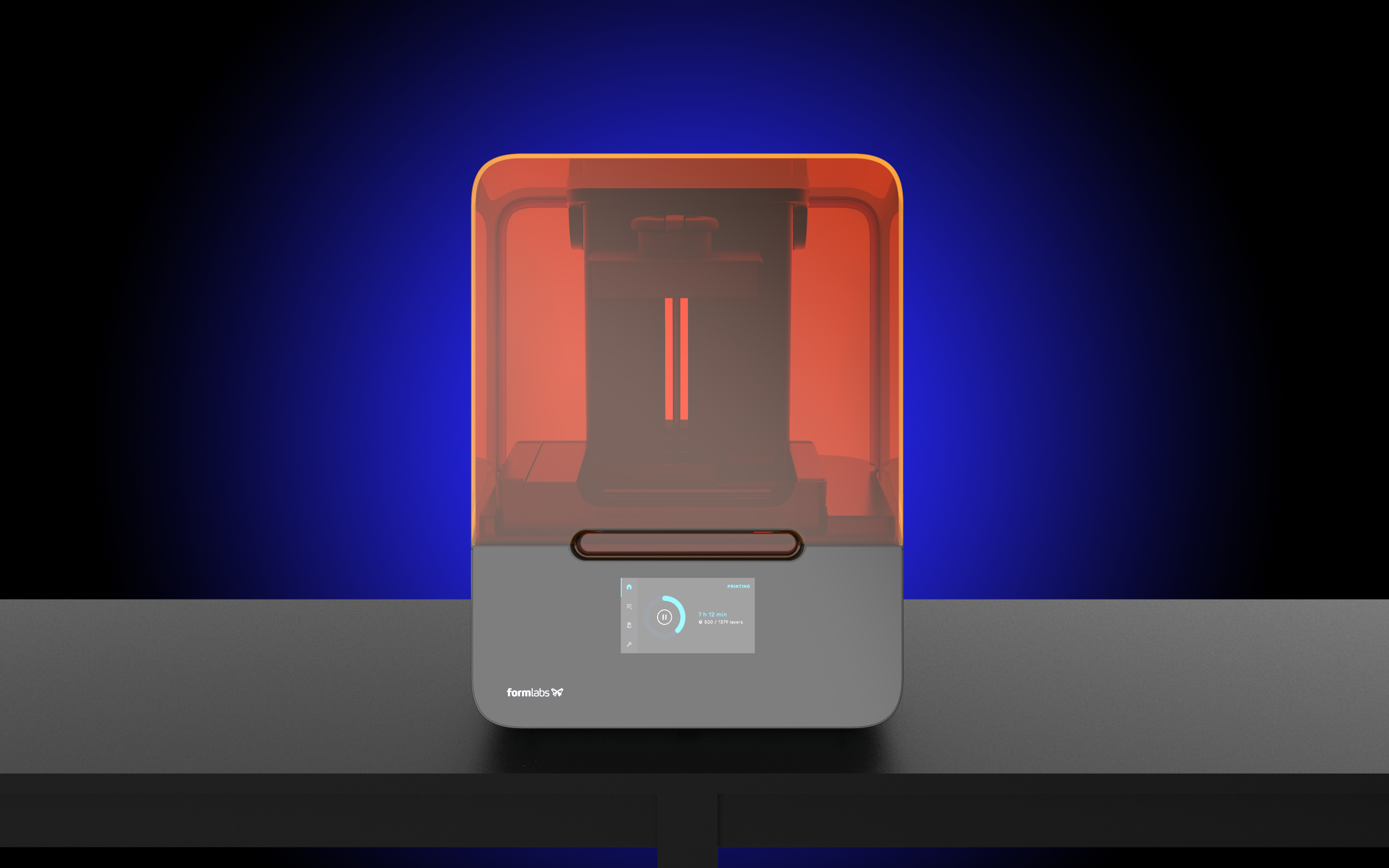